Dressing for a competitive edge
Grinding with higher abrasion rates and at the same time having tools that last longer enables you to save money and deliver faster. This is how you win new customers and outperform competitors – but to do so, everything has to run smoothly.
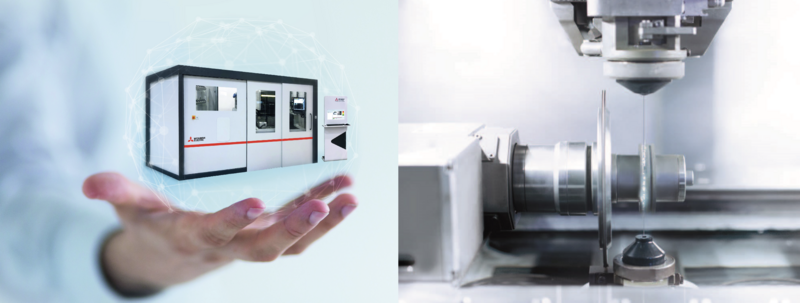
DiamondCell – it’s the right balance of all the components that counts | The grinding wheel is dressed by EDM with high abrasion rates and precision and long tool life
The dressing (= profiling and sharpening) of grinding wheels by EDM is not a fundamentally new technology. However, with the current wire-cutting systems from Mitsubishi Electric, the scope for machining has been extended considerably. Unlike conventional dressing with fixed or moving dressing tools, the process with wire-cutting is contactless. Although this also applies in principle to diesinker dressing with shape-imparting electrodes, the wire erosion process is much kinder to the grinding wheel.
Child’s play with the wire erosion systems from Mitsubishi Electric
The wire erosion systems from Mitsubishi Electric make this process child’s play. The basis is the grinding wheel’s geometry – defined either in a drawing or, better still, in a geometry file, e.g. in DXF format. The profile is programmed as a cutting path. If a DXF file is available, it can be read straight into the control and processed into an NC program. The machining technology is selected from the machine’s database, and then the grinding wheel is clamped and work can start. The process takes place fully automatically, and the only thing left to do is remove the ready-profiled grinding wheel from the chuck. It couldn’t be simpler or more flexible. In cooperation with ITS-Technologies, various rotary spindles have already been developed with the most widely used chuck seats so that grinding wheels of many different sizes and with conventional chuck interfaces can be efficiently processed. Mitsubishi Electric and ITS-Technologies have wide-ranging expertise and plenty of experience in this sector.
DiamondCell – fully automated operation
The process as such is defined and takes place dependably on the unmanned wire EDM machine. This means that a basic precondition for the further automation of this machining technology has been satisfied. Here, again, Mitsubishi Electric has the associated expertise and also the requisite products of its own, e.g. the robots of the MELFA series. Many fully automated machining cells that also dress grinding wheels in self-controlled operation are already in operation. On GrindingHub exhibition in Stuttgart (Germany), Mitsubishi Electric presents in hall 9 booth 9C20 a DiamondCell for fully automated profiling of grinding wheels with a diameter of up to 200 mm.
Technical advantages
• Reproducible dressing results |
• Complex geometries can be produced, hence fewer grinding wheels needed in some cases |
• Intricate structures are easily produced – extension of the scope for grinding |