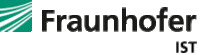
Fraunhofer Institut für Schicht- und Oberflächentechnik IST
Institutional description
As an innovative and internationally recognized partner for research and development, we at the Fraunhofer Institute for Surface Engineering and Thin Films IST develop sustainable products including the associated competitive and scalable production systems.
Our research encompasses plant engineering, entire process chains of process engineering, process and manufacturing technology up to the consideration of entire factories. Based on the requirements of sustainability, we keep an eye on the entire product life cycle - from material to process to component and product to recycling.
In interdisciplinary teams and based on our technology and competence fields, we offer our customers from industry and research customized and sustainable solutions for various sectors, e.g. plant and mechanical engineering, tools, vehicle construction, aerospace, energy, optics, medical and pharmaceutical process engineering, environmental technology, chemistry and digital economy.
Based on a broad spectrum of expertise, technologies, processes and coating materials, we design the optimal process chain for the respective task, all the way to the digital design of the entire factory.
Focal points of the Fraunhofer IST are:
- Diamond-based systems and CleanTech
- Process and manufacturing technology for sustainable energy storage
- Tribological systems
- Sensor technology
- Flexible production systems
- Optical systems and applications
- Simulation & Digital Services
- Interfacial chemistry and adaptive adhesion systems
- Microstructuring
- Analytics and Test Engineering
We apply our expertise in a wide range of technologies for coating, treating and structuring surfaces. These include:
- Electrochemical processes, in particular electroplating
- Atmospheric pressure plasma processes
- Low pressure plasma processes with the main focus on magnetron sputtering, highly ionized plasmas and plasma activated vapor deposition (PECVD)
- Chemical vapor deposition with the main focus on hot wire CVD
- Atomic layer deposition ALD
- Chemical, mechanical and thermal surface treatment
In addition to this the Fraunhofer IST not only has excellent capabilities in surface analysis and quality assurance using the very latest equipment but has also accumulated extensive experience in the modeling and simulation of both product properties and the associated processes and production systems. Further competences include the design of sustainable production and factory systems as well as life cycle engineering (life cycle costing, life cycle assessment).
Productinformation
The deposition of polycrystalline diamond coatings by hot-filament activated vapor deposition (hot-filament CVD, HFCVD) is one of the core competences of the Fraunhofer Institute for Surface Engineering and Thin Films IST. The institute is home to the world's largest hot-filament CVD coating facility for the production of diamond coatings on areas of up to 0.5 x 1m2. This enables us to coat complex tools and components with the highest quality and economy.
CVD diamond coatings have properties comparable with natural diamond
and are characterized by maximum hardness (up to 10,000 HV), extreme wear resistance, minimal friction values and high chemical resistance. The unique material properties provide significant performance improvements and long-lasting products and tools.
The design and manufacturing of CVD diamond coatings, which includes specific treatment sequences, i.e. material selection and characterization, pretreatment, coating and process development and qualification, as well as the application, has already been successfully implemented at the Fraunhofer IST for many years. Depending on the task we offer solutions for cutting tools (turning, milling, grinding, honing), for forming tools or for highly stressed parts and components. In addition, we have many years of expertise in the development and application of other tool coatings, such as diamond-like carbon (DLC) or PVD hard coatings
Tools with specific cutting edge
For milling, turning and drilling tools made of carbide we are developing application-oriented diamond coating systems and pretreatments at the Fraunhofer IST, which, for example, also enable the coating of high-cobalt or alternative carbide grades. We are researching interlayer systems acting as cobalt diffusion barriers, through which etching pretreatment can be substituted and greater degrees of freedom for the selection of suitable carbide grades can beachieved. Other examples include:
- Diamond coating of ceramic tools (DiaCer®).
- Coating, material and wear analysis
- Diamond coating of cobalt-free carbides with alternative binder
- Additional functional and hard material coatings, e.g. as running-in layer or for improved anti-adhesive properties
Grinding tools
The Fraunhofer IST has developed the compeDIA® abrasive coating as an innovative solution for precision grinding tasks. The finest grit sizes down to the submicrometer range enable ductile grinding, the highest surface finishes and low edge zone damage. Due to the one hundred percent diamond content, grinding ratios of up to G = 30 000 and maximum tool life are achieved. Resharpening is possible through cost-effective recoating. In addition, micro mounted points with the smallest diameters down to 50 μm can also be produced, which demonstrate excellent tool life and surface qualities, e.g. when machining zirconia ceramics, quartz glass or steel.
The combination of a structured base body and a highly wear-resistant CVD diamond layer is another research topic that has already been successfully demonstrated in the field of micro mounted points and also for honing stones.
Forming tools
As an alternative to wire drawing dies with solid diamond inserts we are developing special processes, allowing thedepostion of CVD diamond coatings on the inner face of cemented carbide dies . In this way diamond drawing dies with complex cross-sectional profiles and internal diameters from 1mm to over 50mm can be produced. In addition, we develop and evaluate CVD diamond coatings for extrusion, sheet metal forming as well as metal cutting.