Nawa - We search every second
Voith Turbo has switched to NAWA PCD milling cutters and CBN reamers
Voith Turbo has switched the 24/7 roughing of the transmission housings to NAWA's hpcCUT series with brazed PCD cutting edges. Since then, shorter cycle times have been achieved in Garching and tool costs have been significantly reduced. Reaming of valve seats has now also been taken over by NAWA CBN reamers specially designed for this process.
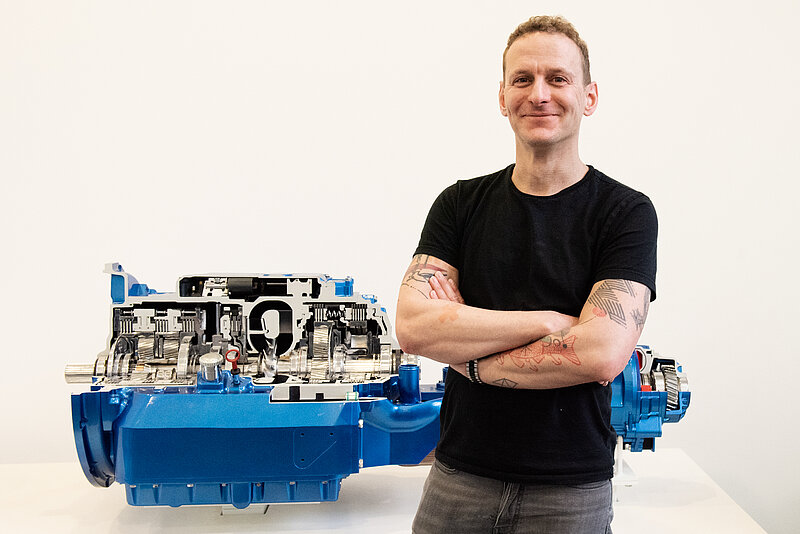
Steffen Seifert in front of the model of the DIWA.6 automatic bus transmission: ‘The machinist doesn't have time to worry about tools that aren't running smoothly.’
We encounter products that have a direct or indirect connection with Voith every day, without realising it. Perhaps when we switch on the light, because around a quarter of all hydroelectric power plants worldwide are equipped with technology from Voith Hydro. Or when we see a book, read an instruction manual, see packaging or use toilet paper – Voith Paper is one of the largest international system suppliers for the paper industry. We are talking about the Voith technology group, which employs around 20,000 people worldwide. A company that has been family-owned for over 150 years and is headquartered in Heidenheim an der Brenz, north of Ulm. Voith Turbo is the third division, complementing the Hydro and Paper divisions. It supplies a wide range of mechanical, hydraulic, hydrodynamic and electric drive and braking systems to a variety of industries. Its areas of application include raw material extraction and processing, as well as classic industrial applications and water, rail and commercial vehicles, including buses. An important manufacturing site is located in Garching, north of Munich.
Complete machining in a 24/7 rhythm
In Garching, the housings for the automatic bus transmissions of the DIWA series, among other components, are machined. ‘On our automatic production line, we machine three DIWA transmission types with different housing variants in 24/7 operation. Plus the housing for the DIWA NXT mild-hybrid bus transmission, which is constructed completely differently,’ says Steffen Seifert from the NC programming department, describing one segment of the huge production spectrum. The housings are made of the aluminium casting alloy GD-ALS110, which is completely machined and thus ready for assembly when it leaves the line. ‘Complete means for us milling, i.e. from roughing to finish machining to final dimension, drilling, chamfering as well as thread production – all in three clampings.’ This task is performed by the three 5-axis horizontal machining centres Heller MC 20, which are arranged next to each other in the production line of the manufacturer Felsomat and are supplemented by a parts washing system. A jointed-arm robot whirs back and forth on rails and, instructed and controlled by the cell computer, serves the three machines, the washing system and the storage locations. ‘For us, it's about the shortest possible cycle times, combined with consistently high machining quality. But that also means absolute process reliability,’ says Seifert, summarising the key points in housing machining. ‘One of the most important factors here is the tools,’ emphasises the NC specialist, who, together with his colleagues from the CAM department in Garching, is also responsible for tool management. A relatively recent example of where a change to a different tool provider would have resulted in a significant increase in productivity was the roughing of the gearbox housings and the reaming of thread seats. And that's how it came about.
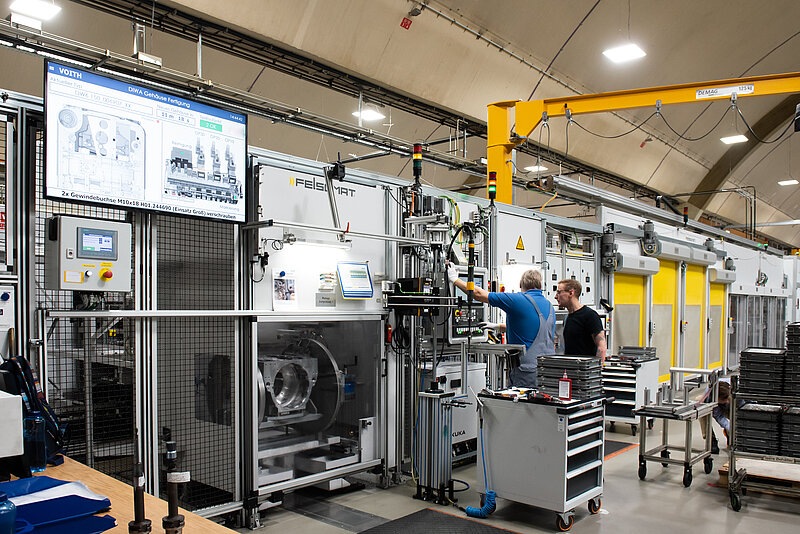
Designed for 24/7 operation: three 5-axis horizontal machining centres (Heller MC20) are arranged next to each other on the production line (Felsomat), supplemented by a parts washing system. An articulated arm robot moves between the stations on rails. A large monitor visualises the currently running processes in real time.
Milling is done exclusively with PCD
Voith purchases its tools from numerous suppliers, including the Franconian manufacturer EMUGE-FRANKEN, which has been one of Voith's suppliers for many years. This also applies to the gearbox housings, the tools for thread cutting or, more recently, the TAPTOR, which is used to create the core hole and the thread in a single operation. Until about a year and a half ago, however, only products from other manufacturers were used for milling. ‘However, we had problems with vibrations, tool life and power development on the component during roughing with a 63mm PCD cutter head,’ says Seifert, describing the initial situation. PKD because, with cutting edges made of extremely hard and wear-resistant polycrystalline diamond, it is possible to achieve a tool life that would never be achieved with solid carbide tools (VHM), says Seifert when asked why these significantly more expensive tools are used to mill cast aluminium. A solid carbide tool was out of the question simply because of the cutting values.
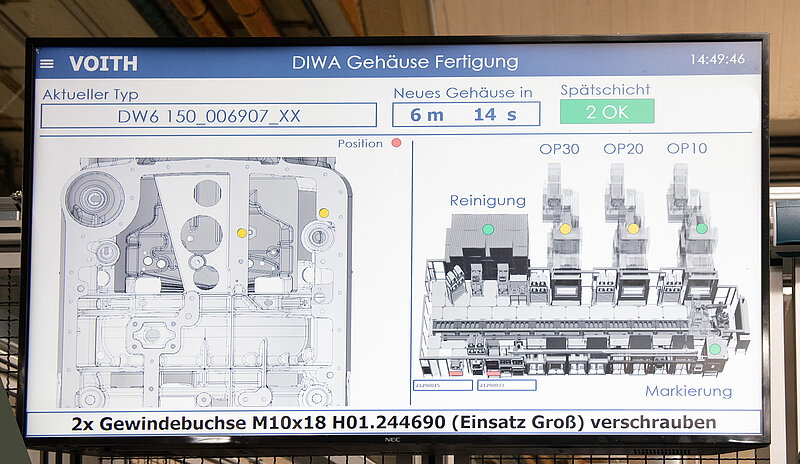
Desire for an alternative
Despite the high-quality PCD inserts, the 63-mm cutter head still caused difficulties during roughing. The CAM specialist recalls that attempts to get to grips with these difficulties with the help of the good manufacturer support did not lead to any significant improvement. There were also vibration problems, which he believes were related to the cutting angle of the blades. Seifert approached Armin Kusch, the local sales representative of EMUGE-FRANKEN Voith, who regularly visits the company in Garching. He had an idea on the subject and suggested that Seifert bring a PCD-tipped 63-mm high-performance face milling cutter in a monoblock design from NAWA for test purposes during his next visit. Seifert had expressly insisted on extensive tests in advance of a possible application under real production conditions.
NAWA Präzisionstechnik is a medium-sized, highly innovative toolmaker based in Veringendorf in the Swabian Alb region of Germany. NAWA has been a subsidiary of EMUGE-FRANKEN for several years. An important product range of the Swabians are PCD-tipped high-performance face mills and shoulder milling cutters from the NAWA hpcCUT series. The PCD inserts are firmly soldered to these monolithic milling cutters. ‘You could say that it is a round plate with milled insert seats, in which the cutting edges are soldered and then ground,’ says Kusch, describing the design. The other end of the HSS milling body is equipped as standard with an HSK-A63 interface and an internal coolant supply in the hpcCUT series. Therefore, no additional holders are required for spindle holders of this type, and the hpcCUT milling cutters can be exchanged directly into the HSK-A63 interface of the machine. This is also the case with two of the three Heller machines in the 24/7 production line in Garching. ‘Thanks to the high number of teeth and the high cutting speeds typical of PCD, these monolithic milling cutters achieve enormous feed rates and thus high material removal rates,’ says Kusch, summarising the features of the hpcCUT series. The 63-mm milling cutter intended for Garching had twelve PCD cutting edges, whereas the indexable milling cutter used there previously had only six.
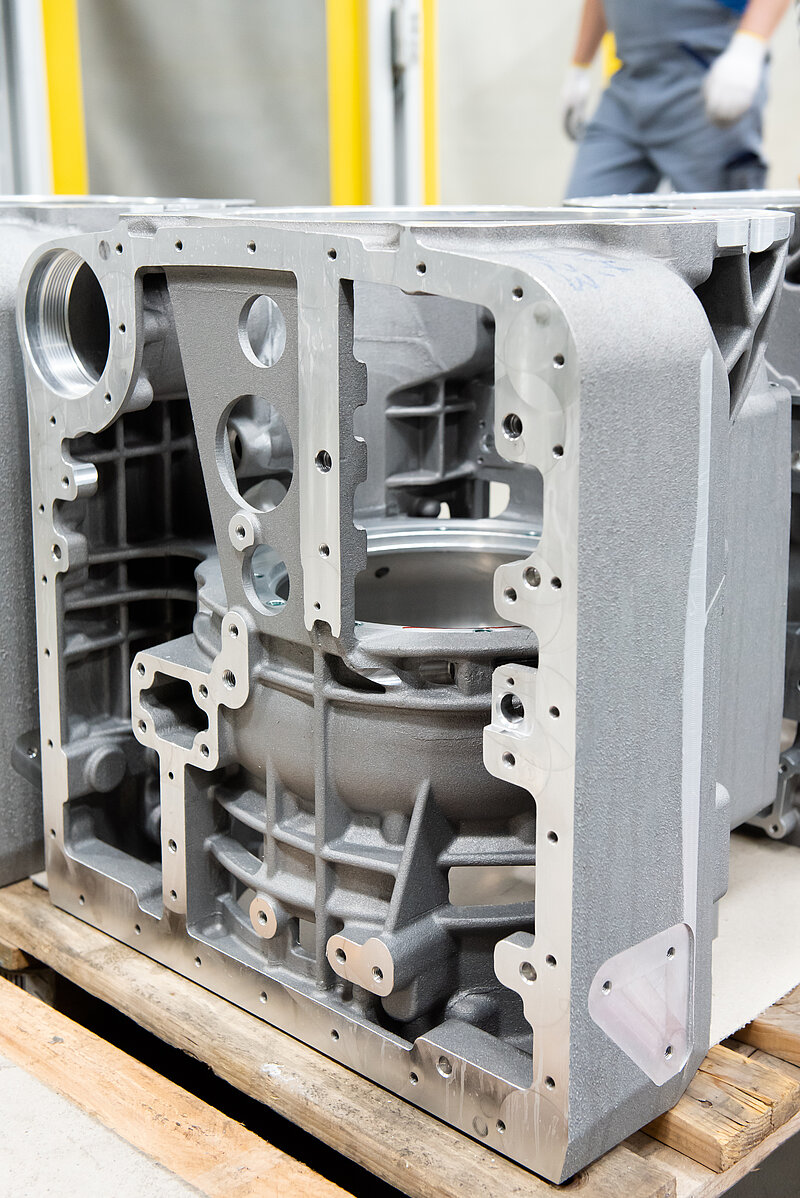
Machined housings for the DIWA automatic bus transmission made of cast aluminium GD-ALS110. Roughing with the hpcCUTPKD milling cutters from NAWA removes about 50 kg of material per housing.
Test results were convincing in all disciplines
The hpcCUT milling cutter from NAWA seemed to be an interesting and, above all, better alternative to the previous reversible cutterhead. This was confirmed by the extensive tests that Seifert and his colleagues then carried out with this PCD milling cutter. ‘The thing worked straight away,’ says Seifert. The cutting values, which we had successively worked towards, were so convincing that we said we would buy the test tool and use the 63-mm hpcCUT milling cutter in series production in the near future. With the predecessor tool, the component was roughed in two cuts to compensate for the dimensional fluctuations of the raw casting, which can sometimes be up to 10 mm. This strategy was retained with the NAWA tool. ‘We have significantly increased the cutting values so that we are almost twice as fast.’ The spindle forces that occur are also significantly lower than with the predecessor tool. The same applies to the vibrations. ‘This is because the NAWA milling cutter is much more aggressive with the cutting angles.’ This is an aspect that is extremely important to Seifert. ’If I introduce vibrations into the housing during scaling, I can no longer get rid of them during finishing because the finishing tool follows these vibrations on the web.’
The monolithic 63 mm milling cutter worked so well that a further PCD tool from the hpcCUT series from NAWA with a diameter of 100 mm was ordered. This was also for roughing, but this time as a shell mill. In other words, a head with 12 PCD cutting edges, also brazed on, that is screwed onto a holder.
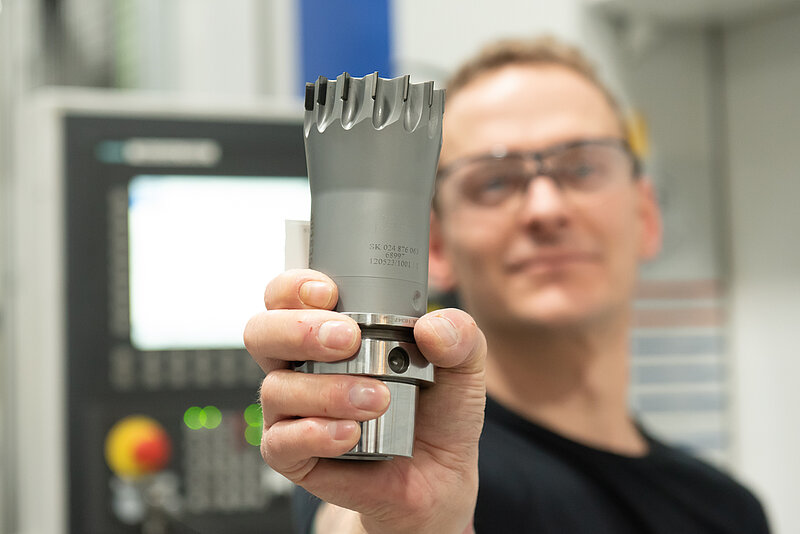
Extremely high performance at a moderate price: the monolithic 63 mm face milling cutter from the NAWA hpcCUT series with an HSK-A63 interface has 12 PCD cutting edges that are firmly soldered. Monoblock tools are part of the standard NAWA range and are available at short notice.
Changeover for reamers too
And there was another machining field in Garching that was eventually switched to the NAWA manufacturer. Namely, the reamers. These are used to ream three 18 mm fittings to final size in a grey cast iron housing (GG-25). In this case, not on the new production line, but on a horizontal 4-axis Heller MCi 16, which is also automated. The tolerance is H7, i.e. 0 + 18 μm, with a surface with an average roughness Rz of 9 μm required, which roughly corresponds to a mean roughness Ra of 1.8 μm. ‘These are the valve seats for the converter outlet valve, which is why the surface quality requirements are so high,’ explains Christian Bauer, one of Seifert's colleagues from the CAM department. As an NC programmer and tool specialist, he is responsible for reaming in Garching, among other things, and was therefore involved in the search for a possible new supplier of reamers from the outset. Possible because they were not actually dissatisfied with the previous tools in terms of process reliability, accuracy and surface quality, but would have liked a longer tool life. ‘The prerequisite for making the switch was that we would be able to adopt the cutting data of the predecessor tool, with which we were already doing very well, one-to-one.’ For finish machining, this means a speed of 3,200 rpm at a feed rate of 4,300 mm/min. The NC program should therefore remain largely the same. Previously, after drilling, two reaming operations were carried out: in the first pass to pre-machine from 17.6 mm to 17.8 mm, and then with the main tool in the second stage from 17.8 mm to the final dimension. This is why a step reamer is used here. ‘NAWA has based the design of its reamer on our approach.’ However, with one small change: ‘NAWA had the idea of increasing the diameter at the beginning of the pre-machining to 17.7 mm.’ The NAWA face reamer is now used in step one from 17.7 mm to 17.9 mm and then from 17.9 mm to the final dimension of 18 mm. Accordingly, Bauer only had to change the allowance, i.e. the amount of material to be removed during reaming. This idea, combined with a cutting edge geometry specially optimised for the application, would have significantly increased the service life of the reamer, Bauer emphasises. And with the same process reliability as its predecessor. The cutting edges are CBN-coated, i.e. with an extremely wear-resistant polycrystalline cubic boron nitride.
The goal was achieved and the Swabian tool manufacturer was awarded the contract. ‘It should also be mentioned that numerous manufacturers have tried this project, but only NAWA had managed it.’ Bauer speaks of a service life gain of about 30 percent. ‘The reamer from NAWA lasts longer and is both cheaper to buy and to recondition than our previous supplier.’ Mr Seifert, who has also had very good experiences with the NAWA maintenance service for milling cutters, agrees. Not only is the purchase price of the milling cutters lower than the previous tool, but NAWA is also cheaper to process, ‘even though these had inserts that can be changed.’
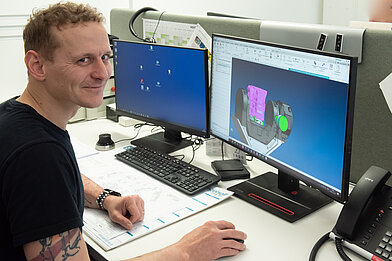
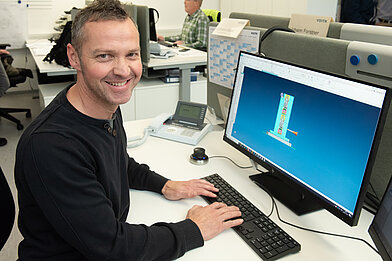
Steffen Seifert and Christian Bauer at their CAM workstations. The NC programs for the machining centres are generated with Siemens NX. The open windows show the swivelling table of the Heller MC 20, and at Christian Bauer's workstation the clamped grey cast iron housings for drilling and reaming on the Heller MCi 16.
Time savings in all directions
NAWA's PCD milling heads have now been in use for about a year and a half, and so far, Seifert says, they are very satisfied. ‘With a comparable service life to the earlier reversible milling cutter, we now have lower tool costs and shorter cycle times.’ Thanks to the HSK-A63 interface, the elimination of tool presetting should not be neglected with the 63 mm monoblock milling cutter. ‘I unpack the NAWA tool, enter the supplied measurement protocol and put it in the machine's magazine or in the replacement cabinet.’ This is because the tools are delivered fully measured, along with the enclosed measurement protocol. Seifert sums up the advantages: time savings in all directions and for everyone involved. ’Because we are looking for every second.’
Source | NAWA Präzisionstechnik GmbH