Next Level Grinding – innovative solutions for a sustainable future
The grinding expert is to present innovative solutions and responses to various challenges facing the industry
Grinding, finishing and dressing – with high-precision, economical solutions which also help to make customer processes more sustainable. As an innovative provider of solutions, Saint-Gobain Abrasives – the leading expert in grinding solutions – supports industrial production with a complete range of products. At Grindtec 2022, the company will be presenting the latest innovations and developments with its Norton and Norton Winter brands. For example, the new Norton Quantum PRIME self-sharpening ceramic grain produces real leaps in performance. In many grinding applications, such as internal-diameter, gear and tool grinding, Saint-Gobain Abrasives is presenting advanced ‘powerhouses’ that are redefining the limits of performance in impressive style.
Norton Quantum PRIME high-performance grinding tools can be used for a wide variety of applications. These include external-diameter, internal-diameter, creep-feed, flat and double-sided face grinding as well as saw sharpening and roll, centreless and flute grinding.
artin Büsch, Head of Marketing for Germany, Austria and Switzerland at Saint-Gobain Abrasives, said, ‘Our grinding solutions have to meet the ever increasing demands of our customers. The tools used need to be capable of working better, faster, and more economical while delivering maximum quality. At the same time, sustainability is becoming an increasingly decisive factor in the development and application of grinding solutions. In the light of our common challenge of finding solutions for tackling climate change and decarbonising industry, the question of how energy demands and CO2 emissions in industrial manufacturing processes can be reduced through the use of innovative abrasives, is of vital importance. For this purpose, Saint-Gobain Abrasives offers comprehensive services and tailored packages of solutions for all applications. We are continuously enhancing and refining them in order to improve their efficiency and precision and thereby the sustainability of the processes as a whole.’
Innovative grain technologies for greater productivity
One example are the Norton high-performance grinding wheels of the new Norton Quantum PRIME generation. The aspiration for tools equipped with Quantum PRIME is to set new standards in a wide range of industries and applications, such as in external-diameter, internal-diameter, creep-feed, flat and double-sided face grinding as well as saw sharpening and roll, centreless and flute grinding. At Grindtec, Saint-Gobain Abrasives will present the unique wheel life enhancing, self-sharpening effect of the grain. Visitors can find out in detail about the significant leaps in performance in combination with the appropriate bond matrix – as in the Norton VITRIUM3, for example.
A further trade fair highlight in grain technology will be AltosX. With the new generation of Altos long extruded shaped grain, Norton is revolutionising grinding in many areas of industrial metalworking. The special combination of long extruded shaped grain and new microstructure offers an extremely high material removal rate and machining volume whilst minimising power consumption, which results in considerable cost savings in high-precision grinding, such as in creep-feed and flat grinding.
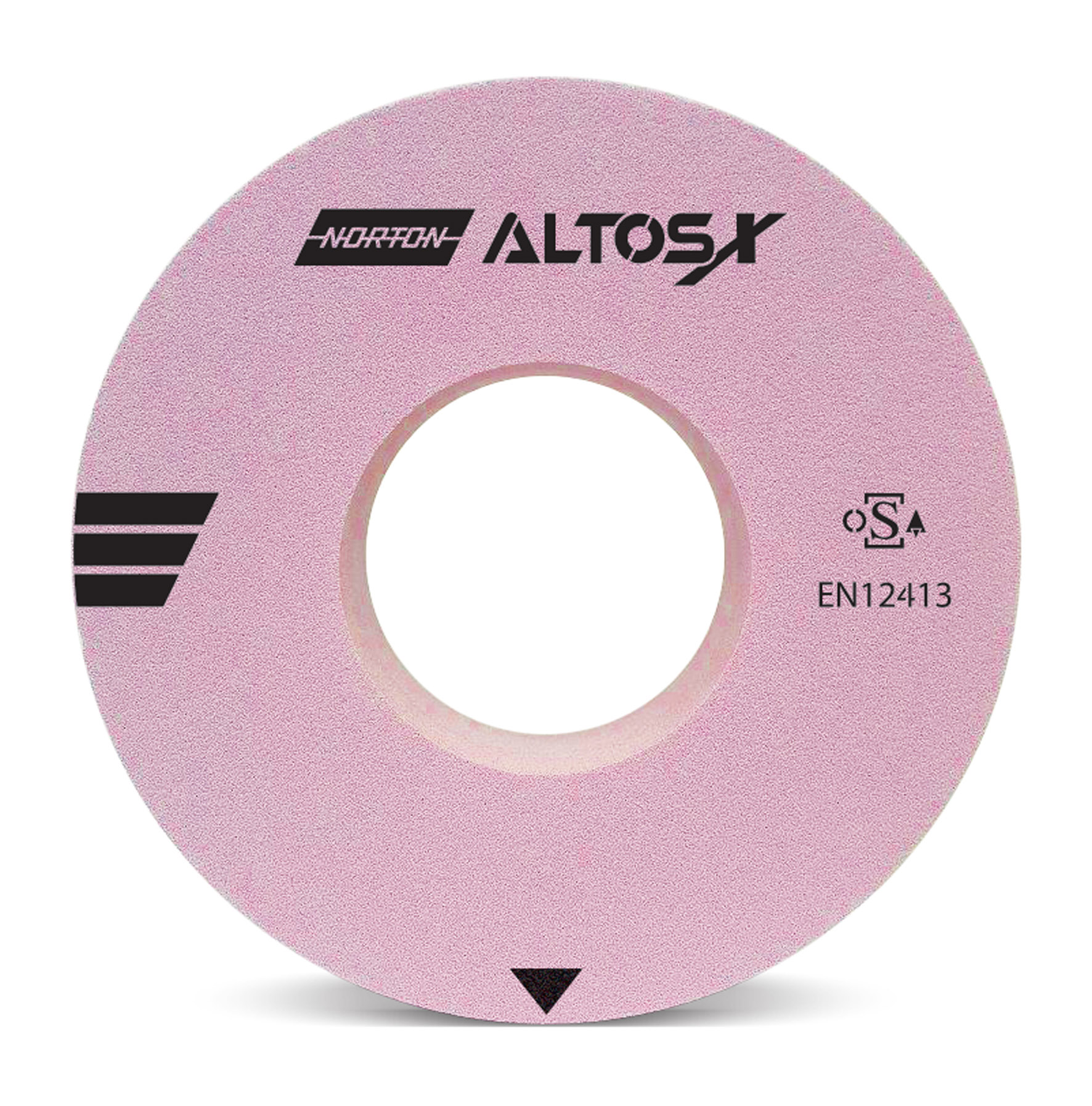
AltosX is more efficient than any other wheel on the market and delivers a removal rate that is twice as high while maintaining the same power consumption. The natural porosity ensures better coolant diffusion and balancing of the wheel, while the even grain distribution guarantees a more stable cut.
Advanced bond formulae
Another focal point at the trade fair will be Norton Winter PARADIGM. Diamond grinding wheels made from this highly porous metal bond enable remarkable results in the grinding of carbide, ceramics, quartz and ferrites. Dr. Stefan Kemethmüller, Sales Director for Engineering Markets in Germany, Austria and Switzerland, commented, ‘The new bond formula outshines usual superabrasive grinding tools and standard hybrid tools that are available on the market. It combines all the benefits that allow a user to machine even tough materials with low power consumption and a much reduced grinding time in a reliable process and to obtain high-quality results.’
As an innovation in the area of ceramic-bonded CBN grinding wheels, Saint-Gobain Abrasives will present the VITRON7 ceramic bond at GrindTec. Thanks to the uniquely homogeneous grain distribution in combination with the porous bond, CBN grinding wheels equipped with Vitron7 are far more productive. The positive characteristics of the new ceramic bond system ensure particularly cool grinding that protects the workpieces and safeguards material integrity. At the same time, the outstanding cutting ability and the significantly extended service life bring about a considerable increase in performance, such as in aircraft manufacturing as well as in the automotive and tool industries.’
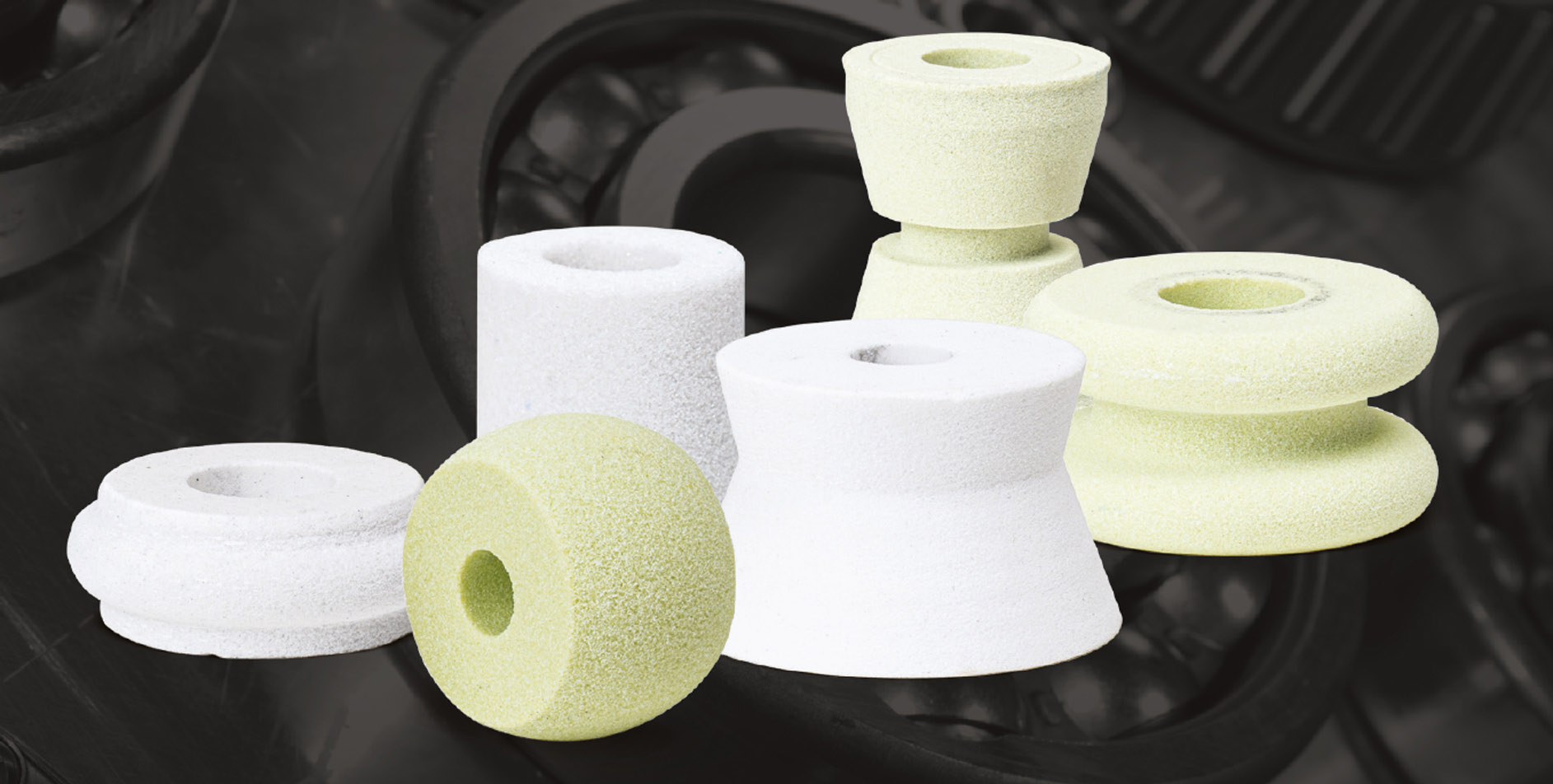
Whether manufacturing roller bearings, gear wheels for gearboxes and automotive components or in tool and mould production, with Norton IDeal Prime, the latest generation of internal diameter grinding wheels, Saint-Gobain Abrasives is providing manufacturers in the precision markets with a high-performance tool that significantly improves productivity as well as component quality and reduces process costs.
Innovative solutions for gear grinding
With Xtrimium, Norton has created a technical platform for designing grinding wheels with a focus on their specific purpose, for roll, profile, worm and bevel gear grinding, for example. Taking individual customers’ intended applications, the mechanical requirements and process reliability into account, the abrasive grain, bond, structure and hardness of the grinding tool are designed precisely for the machining process in question. One example is the Norton Xtrimium dual-worm grinding wheel, which is a unique grinding solution. It fulfils both the actual grinding task of removing material and – with a separate area and a specification adapted accordingly – polishing grinding. In other words, it combines two machining processes in a single clamping operation. As a result, there is no need for retooling and adjustment work, production time is reduced and quality is increased significantly.
In addition to the Xtrimium platform for gear grinding, GrindTec will also how Saint-Gobain Abrasives advanced grinding solutions for the foundry market segment. With the new Foundry X electroplated single-layer grinding wheels, foundries can improve productivity, product quality and the safety of their employees in one fell swoop. Unparalleled grain quality, maximum homogeneity in the coating and an outstanding service life are just some of the many benefits of using Foundry X. Furthermore, Foundry X offers foundries many advantages in comparison with standard electroplated tools, but especially compared with regular, conventionally bonded abrasives, and therefore good reasons to switch to the new Norton Winter diamond and CBN grinding tools. In order to minimise waste and promote sustainability, Saint-Gobain Abrasives offers its customers the opportunity to recoat Norton Winter Foundry X wheels.
Internal diameter grinding is a particularly challenging discipline. With Norton IDeal PRIME, the latest generation of internal diameter grinding wheels, Saint-Gobain Abrasives is now elevating this process to a new level of performance. IDeal PRIME raises both productivity and component quality, which combine to bring about a considerable reduction in process costs.
Dr. Stefan Kemethmüller commented, ‘With Norton Winter Q-Flute PRIME, we are pointing out to tool manufacturers that there is still scope for enhancing performance in flute grinding of HM shank tools.’ Q-Flute PRIME grinding tools feature an innovative high-performance hybrid bond as well as an optimised combination of profile-holding and free grinding behaviour, making flute grinding much more productive and cost-effective while simultaneously delivering even better quality than the already excellent previous grinding systems.
Free-cutting and cool grinding, the Norton Winter PCX Prime ceramic bond, offers a powerful solution for machining the superhard materials PCD and PcBN in the tool industry. With this efficient diamond-ceramic bond matrix, the challenges in this performance-orientated market environment – i.e. seeking more productivity and better surface quality – can be optimally mastered.
As Martin Büsch pointed out, ‘We could continue listing the innovations that we are presenting at GrindTec almost ad infinitum. The visitors to our trade fair stand can look forward to being inspired with new ways to approach their grinding applications even more effectively and economically. We are eagerly awaiting the opportunity to speak to people face to face and have some lively and engaging conversations.’
Saint-Gobain Abrasives at GrindTec: hall 7, stand 7065 and hall 3, stand 3130.