Mit Hochdruck in die Zukunft – Dr. Müller Diamantmetall und die digitale Transformation
In der dynamischen Welt der Werkzeugproduktion hat sich Dr. Müller Diamantmetall, der renommierte Hersteller von Diamant- und CBN-Schleifscheiben mit Sitz in Weilheim, als ein Pionier der Branche etabliert. Seit Jahrzehnten steht das Unternehmen für erstklassige Qualität und fortschrittliche Technologien. Im Oktober 2022 markierte jedoch ein bedeutender Schritt die nächste Phase in der Unternehmensgeschichte: Die Einführung einer digitalen Produktionssteuerung, basierend auf dem seit Jahren entwickelten, hauseigenen ERP System. Dieses hochmoderne Warenwirtschaftssystem, speziell auf die komplexen Produktionsprozesse von Werkzeugherstellern zugeschnitten, stellte Dr. Müller Diamantmetall vor große Herausforderungen, erwies sich jedoch als ein durchschlagender Erfolg. Während der Begriff Industrie 4.0 die Branche dominiert, hat sich Dr. Müller Diamantmetall bereits einen Platz in der Zukunft gesichert. Das Unternehmen verzeichnet nun die höchste Produktivität in seiner Geschichte – ein beeindruckendes Zeugnis für die Effizienz und Innovationskraft des neuen Systems. In diesem Interview werfen wir einen detaillierten Blick auf die transformative Reise von Dr. Müller Diamantmetall. Wir beleuchten die strategischen Entscheidungen, die Herausforderungen der Systemumstellung und die bemerkenswerten Ergebnisse, die das Unternehmen damit erzielt hat. Erfahren Sie, wie Dr. Müller Diamantmetall mit der Implementierung seines neuen ERP-Systems nicht nur seine Produktionsprozesse optimiert, sondern auch die Weichen für eine zukunftssichere Industrie 6.0 gestellt hat.
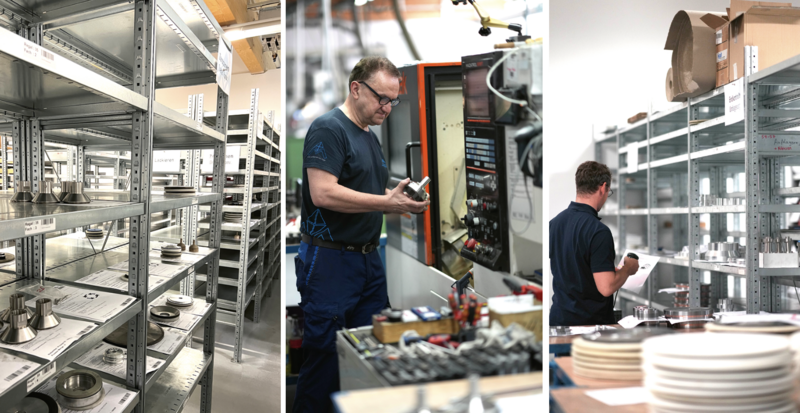
DIAMOND BUSINESS: Im Oktober 2022 begann mit der Einführung eines maßgeschneiderten Produktionssteuerungssystems eine neue Ära für Dr. Müller Diamantmetall. Herr Schulze, Sie haben dieses ERP-System selbst entwickelt. Was waren die Hauptgründe und Herausforderungen, die Sie dazu veranlasst haben, ein eigenes ERP-System zu entwickeln, anstatt eine bestehende Lösung zu implementieren?
Michael Schulze: Oktober 2022 markierte tatsächlich eine Zeitenwende für Dr. Müller Diamantmetall. Die Digitalisierung musste dringend vorangetrieben werden, um mehr Transparenz und Effizienz in unsere Prozesse zu bringen. Als Schleifscheibenhersteller haben wir eine enorme Vielfalt an Artikeln (ca. 130.000 verschiedene Produkte), was den Bedarf an einer großen IT-Abteilung und optimierten Systemen unerlässlich macht. Aber selbst, wenn diese Voraussetzungen gegeben sind, kann man bei hohen Auftragseingängen mit über 40.000 Prozessen dennoch schnell den Überblick verlieren. Die große Menge an Prozessen ergibt sich aus Aufträge x Arbeitsschritte (z.B. 1850 x 22 = 40.700). Durch die Entwicklung unseres maßgeschneiderten ERP-Systems können wir nun sicherstellen, dass unsere speziellen Bedürfnisse vollständig berücksichtigt und in Echtzeit abgebildet werden. Dadurch können wir nun äußerst effizient arbeiten, eine zuverlässige und pünktliche Lieferung garantieren und unser Wachstum nachhaltig fördern.
Aus welchem Grund war es besonders herausfordernd, den Überblick bei hohen Auftragseingängen zubehalten?
Ab einer bestimmten Menge an zu produzierenden Aufträgen herrschte irgendwann Chaos. Viele Unternehmen steuern dies durch manuelle Zwischenlager. Das funktioniert bis zu einem gewissen Punkt, aber bei zu vielen Aufträgen sind die Lager irgendwann voll und das manuelle Sortierungssystem kollabiert. Auch bei uns war das bei einem Umsatz von 10 Mio. Euro der Fall. Denn, in der Regel durchläuft jede Schleifscheibe zwischen 10 und 25 Arbeitsschritte, die alle aufeinander abgestimmt sein müssen. Die Produktionsunterlagen wanderten dann durch die Fertigung, aber bei zu vielen Prozessen wurde es schnell unübersichtlich und das System brach in sich zusammen. Zweimal war es bei uns so weit: 2008 und 2018. Damals war das Auftragsvolumen enorm hoch. In unserer Fertigung laufen normalerweise zeitgleich 1500−2500 Aufträge mit ca. 40.000 Einzelprozessen, wir waren aber bei 3900 Bestellungen mit über 70.000 Prozessen. Die Aufträge standen mit Laufzetteln am Boden und im Regal herum, Prioritäten wurden nicht mehr erkannt und der Überblick ging absolut verloren.
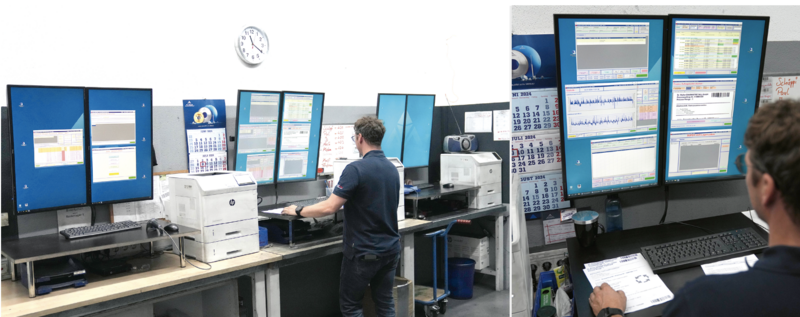
Was hat Sie dazu bewogen, im Oktober 2022 trotz bestehender Lieferverzögerungen das neue Produktionssteuerungssystem einzuführen, obwohl Sie wussten, dass dies Zeit braucht und möglicherweise nicht sofort reibungslos funktionieren würde?
Nachdem ich mich Mitte 2022 von meinem Teilhaber getrennt hatte und wieder alleiniger Geschäftsführer und Inhaber der Dr. Müller Diamantemetall war, erschien mir der Zeitpunkt passend das Unternehmen neu aufzustellen. Es war ein bedeutender Schritt für unser Unternehmen, allerdings auch eine riesige Herausforderung für mich und natürlich auch für alle Mitarbeiter, zumindest in den ersten Wochen und Monaten. Wir waren unsicher, welche Störfaktoren auf uns zukommen würden und welche Probleme dadurch möglicherweise entstehen. Aber da wir durch coronabedingte Produktionsausfälle ohnehin eine viel zu lange Lieferzeit hatten, bot sich durch die Einführung des neuen Systems eine Chance auf Besserung. Wir haben die gesamte Produktion angehalten, die bisherige Steuerung deaktiviert und das neue System (wenn auch etwas brachial) implementiert.
Was hat sich durch das neue System nun signifikant verbessert?
Das neue System funktioniert so, dass jede Bewegung und jeder Prozess genau erfasst und in Echtzeit berechnet wird. Hier ein Beispiel zur Veranschaulichung: Angenommen, ein Mitarbeiter arbeitet an einer CNC-Drehbank. Nach Abschluss eines Arbeitsschritts bringt er das Werkstück ins zentrale Lager und scannt seine Maschinennummer ein (zum Beispiel Nummer 34). Sofort berechnet das System alle anstehenden Aufträge für diese Maschine, sortiert sie nach Dringlichkeit (VIP oder bestimmte Termine) und druckt in etwa 20 Sekunden die erforderlichen Unterlagen aus: Zeichnungen, Arbeitsanweisungen und Entnahmescheine für das Lager. Der Mitarbeiter nimmt diese Unterlagen mit zum Arbeitsplatz, wo er das Halbzeug bearbeitet. Nach Abschluss des Auftrags kehrt er zurück, um den nächsten Schritt zu beginnen, und der Prozess wiederholt sich. Das bedeutet, dass wir keine Halbzeuge mehr bevorraten. Halbzeuge werden erst dann hergestellt, wenn es notwendig und sinnvoll ist. Unser System überprüft jede Nacht in einem Zeitraum von 4-5 Stunden aktuell etwa 40.000 Prozesse. Es berechnet, wann die Durchführung Sinn ergibt, damit alle Arbeitsschritte nahtlos ineinandergreifen und somit möglichst kurze Liegezeiten haben.
Was war Ihre größte Befürchtung bei der Umstellung?
Die größte Sorge bei der Umstellung war, dass die beiden Zentrallager, die wir neu geschaffen hatten, nicht ausreichen würden. Zuvor hatten wir innerhalb des Unternehmens eine Vielzahl kleinerer Lagerplätze für Halbzeuge. Nun haben wir festgestellt, dass wir keine großen Lager benötigen, weil alles erst dann gefertigt wird, wenn es sinnvoll ist. In den beiden großen Lagern arbeiten nun Fachkräfte, die die gesamten Prozesse überwachen und verwalten. Die Abläufe werden „Just in Time“ berechnet und umgesetzt, sodass wir durchwegs effizient arbeiten können. Wir sehen bereits vorher auf den Tag genau, wie lange eine Maschine noch ausgelastet ist. Bei unzureichender Auslastung können wir den Mitarbeiter flexibel an einer anderen Maschine einsetzen oder auch die Kapazität erhöhen wenn uns das System dazu rät. Früher war uns das nicht möglich. Da wurden Aufträge aus der fernen Zukunft herangeholt, welche dann ewig als Halbzeug herum lagen.
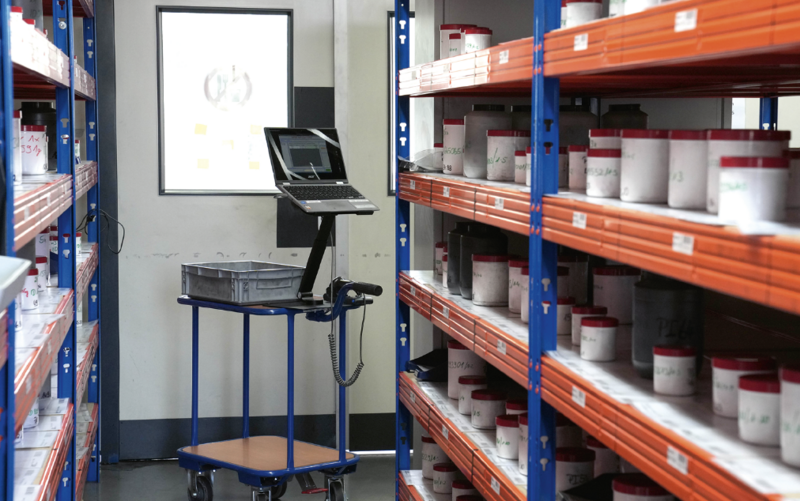
Ist die Auftragslage nun irrelevant für den Arbeitsprozess?
Ob wir nun 1.000 oder 10.000 Aufträge haben, spielt keine Rolle mehr. Alle Prozesse liegen digital in über 60 Maschinengruppen-Warteschlangen und werden erst dann gestartet, wenn der richtige Zeitpunkt gekommen ist, an dem sie ausgeführt werden sollen und können.
Wie lange haben Sie an der Entwicklung und Programmierung der Produktionssteuerung gearbeitet?
Ich habe 3,5 Jahre an diesem System gearbeitet. Damit ein solches System betrieben werden kann, benötigt man umfassende Hintergrundinformationen. Jeder Artikel und jeder Prozess muss minuten- und sekundengenau hinterlegt sein. In den letzten 20 Jahren haben wir all diese Informationen gesammelt und digital erfasst. Mit diesen Daten konnten wir digitale Produktionsablaufpläne erstellen, die dann in die Berechnungen eingeflossen sind. Leider hat es Jahre gedauert, bis alles reibungslos funktionierte und natürlich hätte es schneller gehen sollen, aber die Komplexität des Projekts verlangte diese Zeit.
Wann konnten Sie nach der Umstellung erste positiveErgebnisse sehen?
Tatsächlich war nach sechs Monaten ein deutlicher Fortschritt erkennbar. Die ersten Führungskräfte kamen zu mir und sagten: "Herr Schulze, das funktioniert tatsächlich!". Heute stehen wir vor der großen Anlage und alles läuft reibungslos. Wir müssen keine Aufträge mehr suchen, die schnell erledigt werden müssen. Stattdessen drücken wir auf einen Knopf und planen den Auftrag für übermorgen, und dieser wird termingerecht fertiggestellt. Niemand muss mehr durch die Fertigung laufen und Anweisungen geben. Die Fülle an Informationen, die uns jetzt zur Verfügung steht und die wir für Berechnungen wie beispielsweise für Liefertermine nutzen können, ist wirklich faszinierend. Schlussendlich hatten wir in unserer Firmengeschichte noch nie einen so konstanten Ausstoß an Werkzeugen.
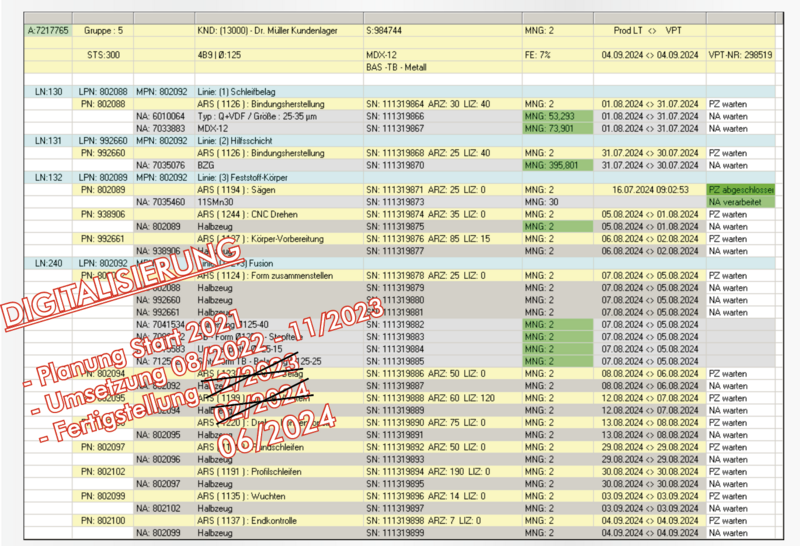
In Ihrer Betriebsgröße und Branche wird die Fertigung oft auf Standard ERP-Systeme umgestellt. Hatten Sie diesen Gedanken nie in Erwägung gezogen? Das hätte Ihnen möglicherweise viel Zeit ersparen können.
Wir hatten vor 15 Jahren genau so eine Standardlösung von einem großen Anbieter. Aber das System machte so viel Ärger, funktionierte nicht richtig und der Service war trotz hoher Kosten schlecht. Und jedes Mal wenn alles einigermaßen am Laufen war, gab es ein neues Release und der Ärger startete von neuem. Unser eigenes System ist nicht nur auf unsere Bedürfnisse zugeschnitten, sondern es enthält auch neben den Standard Modulen wie Artikel, Angebots- und Rechnungswesen auch das neue hier vorgestellte Produktionssteuerungssystem das auf Kapazitäten berechnet. Die Flexibilität und Transparenz, die wir damit bis heute erreicht haben, möchten wir nie wieder vermissen.
Rückblickend betrachtet, würden Sie die Umstellung noch einmal genauso durchführen? Oder anders gefragt, was würden Sie anders machen, wenn Sie die Zeit zurückdrehen könnten?
Ich denke, ich hätte die Umstellung viel besser kommunizieren müssen, sowohl innerhalb des Unternehmens als auch mit unseren Kunden. Das war leider etwas unglücklich. Ich hätte alle Beteiligten frühzeitig einbinden und die Notwendigkeit einer neuen ERP-Einführung deutlicher erklären sollen. Es gab Gründe für die Verzögerungen bei den Lieferzeiten, die den Kunden damals nicht bekannt waren. Jetzt läuft alles deutlich besser und wir alle sind mehr als zufrieden mit der neuen Unternehmenssoftware. Doch jeder, der Erfahrung mit ERP-Einführung hat, weiß, welche Herausforderungen damit verbunden sind und wie lange es dauern kann, bis alles reibungslos funktioniert. Ich bin sehr erleichtert, dass wir diese Phase hinter uns haben und auch dankbar, dass unsere Kunden uns die Treue gehalten haben, trotz dieser schwierigen Phase. Es war eine anstrengende Zeit für uns alle. Die gute Nachricht: Dank des neuen Systems können wir mittlerweile wieder Lieferzeiten zwischen 6 und 8 Wochen realisieren und unsere Kunden wieder von Dr. Müller DIAMANTMETALL überzeugen. Und da wir gerade dabei sind, möchte ich mich aufrichtig bei unseren Kunden entschuldigen, insbesondere dafür, dass wir – oder ich – im Vorfeld nicht ausreichend informiert haben.
Mitarbeiter lehnen Veränderungen eher ab oder tun sich schwer damit. Wie wurde die neue Unternehmenssoftware angenommen?
Ja, das haben wir auch gedacht. Anfangs herrschte Panik, da wir die Prozesse immer wieder anpassen mussten. Die Mitarbeiter standen bei der Einführung herum und wussten nicht weiter. Mit der Zeit hat sich das gelegt. Und jetzt sind sie begeistert und überzeugt, dass dieses System uns nach vorne bringt.
Was hat sich konkret für die Mitarbeiter verändert?
Früher haben sich die Mitarbeiter ihre Arbeit selbst aus einem Regal in der Nähe ihres Arbeitsplatzes geholt. Was dazu führte, dass nicht unbedingt immer der zeitkritisch korrekte Auftrag genommen wurde. Jetzt erhalten unsere Mitarbeiter Ihren nächsten Arbeitsauftrag durch die vom ERP-System täglich neu berechneten Warteschlangen. Eine willkürliche Entnahme wie früher ist nicht mehr möglich. Was heute fällig ist, wird heute auch gefertigt. Erst danach kümmern wir uns um die Rückstände. Früher war es anders, da haben wir erst die Rückstände bearbeitet ...
Warum wird der Rückstand nicht zuerst abgearbeitet?
Ich erkläre es gerne am Beispiel eines Flugplans: Stellen Sie sich vor, Sie sitzen am Flughafen und Ihr Flugzeug hat Verspätung. Die Fluggesellschaft toleriert das vielleicht ein bis drei Stunden. Danach wird Ihr Ticket storniert und Sie müssen nach Hause fahren. Würde die Fluggesellschaft den Flug aufrechterhalten und das Flugzeug irgendwann starten, hätten alle Folgeflüge denselben Verzug wie Ihr Flug. Genau hier liegt das Problem. Durch die Digitalisierung haben wir gelernt, dass wir Aufträge, die stark im Verzug sind, neu terminieren müssen, um die pünktliche Fertigung und Auslieferung der restlichen Aufträge zu gewährleisten.
Nach all Ihren Erläuterungen und meinem laienhaften Einblick in Ihr neues ERP-System: Es klingt alles sehr logisch, folgerichtig und es ist auch sehr anschaulich dargestellt. Können wir hierbei schon von einem Goldstandard sprechen? Beziehungsweise wäre es auch kompatibel für andere Werkzeughersteller?
Sagen wir es einmal so: Wir haben jetzt einen Diamantstandard! Sie werden ein solches System normalerweise nicht in einem mittelständischen Unternehmen mit 85 Mitarbeitern finden. Manchmal kommen wir uns vor wie ein Softwarehersteller der Diamantwerkzeuge herstellt und nicht umgekehrt. Aber die Komplexität der Diamantschleifscheiben-Herstellung hat uns dahin getrieben mit meiner Software so weit zu gehen ...
Neulich sagte ein Bankmitarbeiter zu mir: "Herr Schulze, seien Sie mir nicht böse, aber dieses System ist vielfach mehr wert als Ihr eigenes Unternehmen." Unser neues System ermöglicht es uns, die theoretischen Lieferzeiten auf die Minute genau zu berechnen. Es zeigt genau, wo in den einzelnen Sektoren Engpässe bestehen, berücksichtigt Karenzzeiten und Puffer, und liefert uns dann den präzisen Liefertermin. Diese Fähigkeit hat uns immer gefehlt und ist nun ein entscheidender Vorteil für unser Unternehmen. Darüber hinaus können wir unsere Produktion nun auch virtuell planen. Wir haben die Möglichkeit, den Umsatz des letzten Monats zu skalieren und hypothetische Szenarien durchzurechnen. Zum Beispiel können wir analysieren, wie sich der Umsatz entwickelt hätte, wenn wir eine zusätzliche Maschine gehabt hätten. So können wir die Auswirkungen solcher Investitionen virtuell simulieren und äußerst präzise berechnen. Das ist eine der besten Funktionen an diesem System.
Wenn Sie einen Wunsch für Ihr Unternehmen frei hätten, was wäre Ihr dringendster Wunsch?Es wäre erstrebenswert, zusätzliche qualifizierte Mitarbeiter zu gewinnen. Mit der richtigen Unterstützung sehe ich großes Potenzial, unseren Umsatz von derzeit etwa 10 Millionen auf 20 Millionen zu steigern. Leider ist es in unserer (Urlaubs-)Region eine Herausforderung, geeignete Fachkräfte zu finden, da Wohnraum extrem knapp und damit auch teuer ist.
Worauf liegt Ihr Augenmerk in den nächsten Monaten?
Die Produktion läuft jetzt reibungslos, daher konzentriere ich mich nun auf den Vertrieb, den Verkauf und das Produktmanagement. Diese Bereiche greifen alle ineinander und sind entscheidend für unseren Erfolg. Momentan wird unser Team umfassend umstrukturiert. In Zukunft wird die Arbeitsvorbereitung nicht mehr direkt Artikel bauen, sondern die KI trainieren. Diese KI wird dann die Artikel anlegen und die Prozesse weiter optimieren. Darüber hinaus wird es darum gehen, die Automatisierung nach vorne zu treiben. Mit diesen Erneuerungen wird es gelingen, Dr. Müller Diamantmetall noch zukunftsfähiger und bestens gerüstet für die Herausforderungen von morgen zu machen – zum Wohle unserer Mitarbeiter und unserer Kunden.
Der erste große Schritt ist bereits getan …
Quelle: Dr. Müller