Innovative Methode zur Schneidkantenpräparation
Die Gestalt der Schneidkante ist in der Zerspanung für das Einsatzverhalten der Werkzeuge von zentraler Bedeutung. Sie beeinflusst alle wesentlichen Größen im Zerspanprozess: Die Spanbildung, die thermische und mechanische Belastung des Werkzeugs und des Bauteils, den Werkzeugverschleiß sowie die resultierende Bauteilqualität. Dieser Einfluss ist abhängig von der Größe und Form der Schneidkantenverrundung.
Dieser Einfluss ist abhängig von der Größe und Form der Schneidkantenverrundung. Asymmetrische Verrundungen, wie in Abbildung 1, zeigen je nach Zerspanprozess häufig das größte Potenzial in Bezug auf die Werkzeugstandzeit [1]. Die mögliche Standzeitverlängerung bei optimal ausgelegter, asymmetrischer Verrundung kann 100% beim Drehen betragen, während mit einer symmetrischen Verrundung 50% erreicht werden [2]. Neben der Erhöhung der Standzeit zeigt sich, dass auch die Oberflächenqualität durch eine gezielt ausgelegte asymmetrische Verrundung erhöht wird [2]. Eine an den Belastungsfall und die zu erreichende Bauteilqualität angepasste Schneidkantenverrundung ist in vielen Zerspanprozessen notwendig. Insbesondere bei hochkomplexen Bauteilen und optimierten Prozessketten kann hierdurch ein signifikanter Vorteil hinsichtlich der Produktivität erzielt werden.
Als Methoden der Kantenpräparation finden das Strahlen, das Bürsten und das Schleppschleifen industrielle Anwendung. Eine wirtschaftliche Herstellung lokal angepasster, asymmetrischer Schneidkantengeometrien an Zerspanwerkzeugen mit komplizierter Schneidengeometrie, wie beispielsweise Vollhartmetallwerkzeuge mit Drall und Schneidkantenfasen, ist hiermit jedoch nicht erreichbar [3]. Ein Lösungsansatz ist die Verwendung nachgiebiger Diamantpolierwerkzeuge. In der Prozesskette können diese direkt integriert und in der Werkzeugschleifmaschine eingesetzt werden. Es konnte bereits an Wendeschneidplatten gezeigt werden, dass mit nachgiebigen Diamantpolierwerkzeugen eine hohe Flexibilität hinsichtlich der erzielbaren Mikrogeometrie erreicht wird und eine reproduzierbare Schneidkantenpräparation möglich ist [4]. Innerhalb eines Forschungsprojektes erfolgte am Institut für Fertigungstechnik und Werkzeugmaschinen der Leibniz Universität Hannover (IFW) die Übertragung der Erkenntnisse auf die Bearbeitung von Vollhartmetallwerkzeugen in der Schleifmaschine und das Einsatzverhalten der präparierten Werkzeuge wurde untersucht. Hierbei wurde das Einsatzverhalten der präparierten Werkzeuge untersucht und analysiert. Im Folgenden werden die Erkenntnisse zum Einfluss des Polierverfahrens auf die Werkzeugstandzeit, Prozesskräfte sowie die resultierende Werkstückoberfläche vorgestellt. Dabei wird gezeigt, dass mit einer asymmetrischen Schneidkantenverrundung an der Umfangsschneide der Schaftfräser ein signifikanter Standzeitgewinn erzielt werden kann. Das Verfahren bietet somit ein hohes Potenzial für die Schneidkantenpräparation komplizierter Hartmetallwerkzeuge in der Werkzeugschleifmaschine.
Schneidkantenpräparation mittels nachgiebiger Polierwerkzeuge in der Werkzeugschleifmaschine
Für die Schneidkantenpräparation wurde die 5-Achs-CNC-Schleifmaschine Helitronic Vision 400L der Firma Walter Maschinenbau GmbH eingesetzt. Diese ist mit einem Vierfach-Werkzeugwechsler ausgestattet, sodass eine effiziente Herstellung von Fräswerkzeugen mit integriertem Präparationsschritt realisierbar ist, da eine gleichzeitige Aufnahme aller drei benötigten Schleifscheibentypen sowie der Diamantpolierwerkzeuge möglich ist. In Verbindung mit der Schleifmaschine wurde das Softwarepaket Walter Helitronic Tool-Studio einsetzt. Diese Software ermöglicht es, die für die Herstellung der Fräswerkzeuge notwendigen Programme für die Schleifmaschine automatisiert zu erstellen. Bei den verwendeten Polier- werkzeugen handelt es sich um ein 2-stufiges Poliersystem der Firma EVE GmbH. Sie besitzen einen Durchmesser von 11mm und bestehen aus flexiblen Kunststofflamellen mit eingebetteten Diamantkörnern. Der Aufbau des Polierwerkzeugs unterteilt sich in zwei Lamellenebenen, die sich in der Bindung und Körnung unterscheiden. Die vordere Lamellenebene besitzt eine gröbere Körnung (Korngröße von ca. 20μm) und erzielt damit einen höheren Abtrag an der Schneidkante. Die hintere Lammellenebene realisiert durch die feinere Körnung (Körnung von ca. 4μm) auf der Schneidkante eine bessere Oberflächen- güte in Form einer signifikant niedrigeren Rauheit. Durch die Anordnung der Lamellenebenen wird ein hoher Abtrag sowie eine geringe Oberflächenrauheit an der Schneidkante ermöglicht. Ein Lamellenpaar besitzt eine Breite von ca. 1,9mm. Die Polierwerkzeuge werden in der Regel in der Medizintechnik für die Bearbeitung von keramischen Zahn-implantaten verwendet. Die Werkzeuge können bis zu einer Drehzahl von maxi- mal 20.000min-1 eingesetzt werden. Für die zu präparierenden Werkzeuge wurden gleichgeteilte, unbeschichtete Vollhartmetallschaftfräser mit einem Durchmesser von d = 12mm, einem Drallwinkel von 30°, einem Keilwinkel von β = 69° und einer Zähnezahl von z = 4 gewählt. Im Ausgangzustand verfügen die Fräswerkzeuge sowohl an der Stirn- als auch der Umfangsschneide über eine scharfe Schneidkante mit einer Schneidkantenverrundung S ̅ < 5μm. Der entsprechende Versuchsaufbau ist in Abbildung 1 dargestellt.
Für die Schneidkantenpräparation wurde der Präparationsprozess Parallelpolieren eingesetzt. Hierbei liegen die Lamellenpaare senkrecht zur Schneidkante und die Kontaktfläche am Werkzeug ist an den Polierspitzen. Die Zielgrößen für die durchgeführten Schneidkantenprärationen sind die erzielbare Verrundung auf Frei- und Spanfläche, beschrieben durch die Schneidkantenabschnitte Sα und Sϒ sowie den Formfaktor K. Dabei sind Sα und Sϒ definiert als die Strecke von der Schneidkante einer ideal scharfen Schneidkante bis zum Ablösepunkt an der Span- bzw. Freifläche. Die Verkippung der Verrundung wird durch den Quotienten von Sϒ und Sα angegeben und als Formfaktor K bezeichnet [5]. Symmetrische Schneidkantenverrundungen haben einen Formfaktor von K = 1, asymmetrische Schneidkantenverrundungen mit Verkippung zur Freifläche K < 1. Dementsprechend haben zur Spanfläche verkippte Verrundungen einen Formfaktor K > 1. Zudem wird die mittlere Schneidkantenverrundung S ̅ angegeben als Mittelwert von Sα und Sϒ [4]. Für die Schneidkantenpräparation wurden die Prozesseinstellgrößen so eingestellt, dass die Stirnschneiden mit K < 1 und die Umfangsschneiden mit K > 1 verrundet wurden, um den posi- tiven Effekt unterschiedlicher Verrundungen zu erreichen. Für die Umfangsschneide wurde der Formfaktor K = 1,3 und K = 1,5, für die Stirnschneide ein Formfaktor von K = 0,8 und K = 0,5 gewählt. Ein Formfaktor K < 1 an der Stirnschneide soll zu einer besseren Oberflächenqualität der Bauteile führen. Zusätzlich wurden mit dem Polierwerkzeug die Schneidkantengeometrien mit dem Formfaktor von K = 1 an der Stirn- sowie Umfangsschneide erstellt. Mit dem Polierverfahren kann somit ein Fräswerkzeug innerhalb von einer Minute verrundet werden. Zudem wurden mit der gleichen Werkzeuggeometrie Referenzwerkzeuge mittels Schleppschleifen bei der Firma LMT Fette hergestellt. Die mittlere Schneidkantenverrundung S ̅ lag bei allen Werkzeugen bei S ̅ = 20µm. Die Verrundung am Eckenradius der Fräswerkzeuge war mit der Schneidkantenverrundung an der Umfangsschneide identisch. Nach der Schneidkantenpräparation wurden die Fräswerkzeuge mit einer AlTiN-Beschichtung beschichtet.
Einsatzuntersuchungender polierten Werkzeuge
Die Einsatzuntersuchungen der mit den Diamantpolierwerkzeugen präparierten Fräswerkzeuge wurden auf einem 4-Achs Fräszentrum Typ Heller MC 16 durchgeführt. Für die Fräsuntersuchungen wurden konstante, an den Werkstoff (42CrMo4+QT) angepasste Prozesseinstellgrößen verwendet. Die Schnittgeschwindigkeit wurde auf vc = 200m/min und der Zahnvorschub auf fz = 0,1mm eingestellt. Zur Bewertung des Einsatzverhaltens wurden neben der erreichbaren Standzeit die Prozesskräfte und die Qualität der erzeugten Oberfläche gemessen. Der Verschleiß wurde mit einem Digitalmikroskop Typ Keyence VHX5000 dokumentiert und Verschleißkurven aufgezeichnet. Abbruchkriterium ist eine Verschleißmarkenbreite von VBmax = 200µm oder Schneidkantenausbrüche an den Werkzeugen. Es wurden zwei Wieder-holversuche durchgeführt. Zur Bewertung der Bauteilqualität wurde die Oberflächenrauheit mit einem Mahr Perthometer gemessen.
Beim Einsetzen der verrundeten Werkzeuge wurde deutlich, dass es an der Umfangsschneide mit zunehmender Einsatzzeit Freiflächenverschleiß sowie Kolkverschleiß auf der Spanfläche resultiert. An der Stirnseite bildete sich ebenfalls Freiflächenverschleiß aus. Zusätzlich kam es an der Umfangschneide nach längerer Einsatzzeit zu Ausbrüchen an der Schneidkante. Standzeitlimitierend war in den durchgeführten Zerspanuntersuchungen der Freiflächen- verschleiß sowie die Ausbrüche an der Umfangschneide.
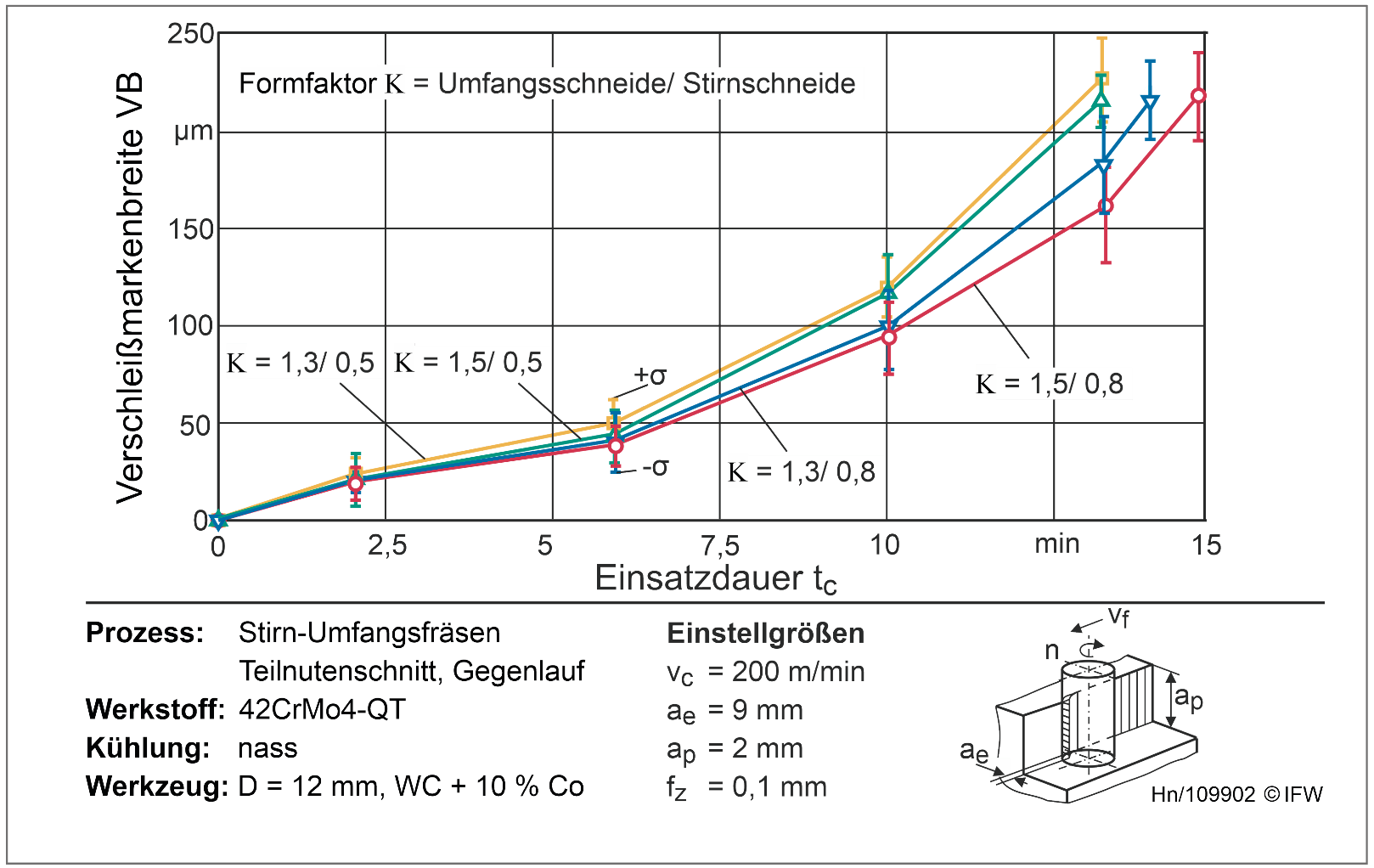
Abb. 2: Einsatzdauer der asymmetrisch verwundeten Fräswerkzeuge
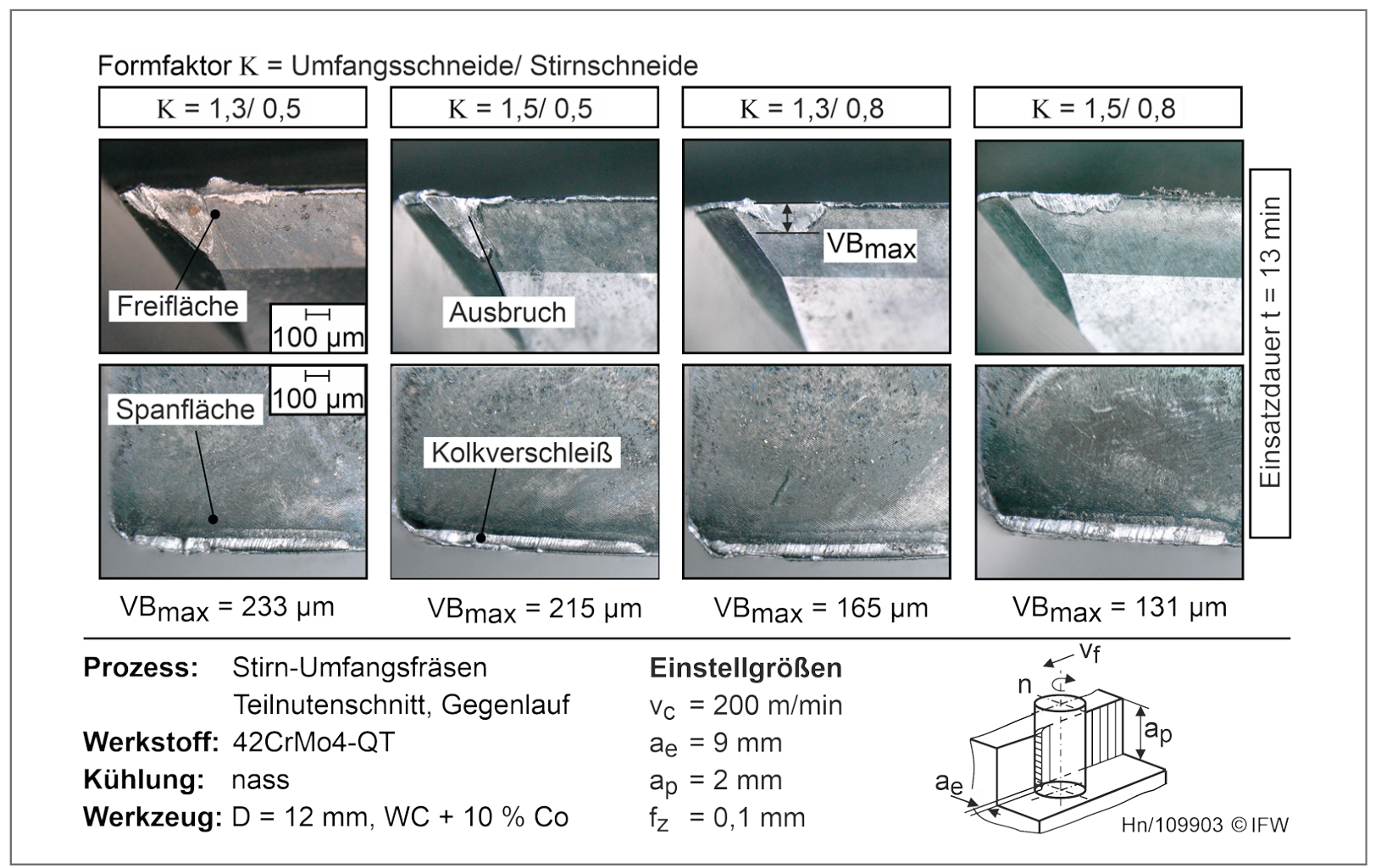
Abb. 3: Verschleiss der asymmetrisch verwundeten Fräswerkzeuge
In Abbildung 2 sind die Standzeiten der asymmetrischen Schneidkanten- verrundungen dargestellt. Es wird deutlich, dass der Formfaktor die resultierende Einsatzzeit der Werkzeuge signifikant beeinflusst. Mit größerem Formfaktor auf der Umfangsschneide resultiert ein geringerer Werkzeugverschleiß und die Standzeit kann erhöht werden. Auch der Formfaktor der Stirnschneide beeinflusst die Werkzeugstandzeit. Bei abnehmendem Formfaktor steigt der Verschleiß an der Stirnschneide sowie am Eckenradius an den Fräswerkzeugen. Durch die asymmetrische Verrundung wird eine Verschiebung der thermo-mechanischen Belastung hin zur Span- bzw. Freifläche erreicht. Vor allem eine Kürzung des Freiflächenabschnitts Sα senkt dabei, aufgrund der niedrigeren Kontaktfläche, die entstehende thermische Belastung an der Freifläche. Ebenfalls wird so die mechanische Belastung im Werkzeug durch die Schneidkantenmikrogeometrie verringert. Eine Erhöhung des Schneidkantenabschnitts S stabilisiert im unterbrochenen Schnitt für die Bearbeitung von 42CrMo4+QT den Schneidkeil. Aus diesem Grund weisen die Werkzeuge mit größerem Formfaktor an der Umfangsschneide eine längere Standzeit auf. Der Verschleiß der Schaftfräser ist in Abbildung 3 beispielhaft nach einer Einsatzdauer von 13 Minuten gezeigt. Dabei wird deutlich, dass die maximale Verschleißmarkenbreite bei den Werkzeugen mit einem Formfaktor von K = 0,8 auf der Stirnschneide nach dieser Einsatzdauer nicht erreicht wurde. Beim Kolkverschleiß auf der Spanfläche der Fräswerkzeuge konnte kein signifikanter Unterschied festgestellt werden. Außerdem ist zu erkennen, dass der Verschleiß bei den Werkzeugen mit einem Formfaktor K = 0,5 besonders stark am Eckenradius ausgeprägt ist. Im Vergleich zu den symmetrischen Referenzwerkzeugen zeigt die asymmetrische Schneidkantenverrundung einen signifikanten Standzeitgewinn (s. Abb. 4). Die symmetrisch verrundeten Werkzeuge erreichen bereits nach 12 Minuten die maximale Verschleißmarkenbreite von VBmax = 200µm. Zwischen den polierten und schleppgeschliffenen Werkzeugen mit einem Formfaktor von K = 1 auf der Umfangs- sowie Stirnschneide ist die resultierende Standzeit nahezu identisch. Dadurch wird deutlich, dass mit dem Polieren als Schneidkantenpräparationsverfahren gleiche Standzeiten der Zerspanwerkzeuge, wie mit andere Präparationsverfahren, erreicht werden können. Die schleppgeschliffenen Werkzeuge zeigen vermehrt Ausbruchstellen entlang der Umfangsschneide (s. Abb. 5). Bei den Fräswerkzeugen, die mit dem Polierverfahren präpariert wurden, kam es hauptsächlich zu einer Ausbruchstelle an der Umfangsschneide, die sich bei fortschreitender Einsatzzeit vergrößerte und zum Standzeitende der Werkzeuge führte. Dies spricht für eine stabilere Schneidkante durch das Polierverfahren im Vergleich zum Schleppschleifen, durch eine Senkung der Schneidkantenschartigkeit mit dem Polieren. Die asymmetrisch verrundeten Werkzeuge mit einem Formfaktor von K = 1,5 an der Umfangsschneide und einem Formfaktor von K = 0,8 weisen nach 13 Minuten Einsatzdauer vor allem Freiflächenverschleiß auf. Einen ähnlich stark ausgeprägten Verschleiß zeigen die Referenzwerkzeuge bereits nach einer Einsatzdauer von 10 Minuten (s. Abb. 5). Hiermit wird ebenfalls deutlich, dass durch eine asymmetrische Verrundung die Standzeit signifikant erhöht wird.