Mit Vision und Willenskraft auf Erfolgskurs
Ceratonia als Rohstoff- und Qualitätslieferant seit 1996 auf Erfolgskurs!
Ungeniert darf man behaupten, dass die Einführung des mittlerweile gängigen CVD-Dickschicht-Diamanten im Fertigungsalltag definitiv ein Verdienst von Reiner Dümpert ist. Vor 25 Jahren gründete er die Firma Ceratonia mit der Überzeugung, diesen überlegenen, aber damals absolut unbekannten Schneidstoff weltweit zu vermarkten bzw. nach Kundenwusch zu konfektionieren. Aus der One-man-show ist mittlerweile ein repräsentatives international agierendes Unternehmen mit knapp 15 Mitarbeitern geworden.
Wer Reiner Dümpert kennt, weiß, dass Geduld nicht seine größte Stärke ist. Visionen im Kopf, immer von neuen Ideen getrieben und durchaus überdurchschnittlich risikofreudig – so könnte man ihn mit kurzen Worten beschreiben. „Als ich 1997 die ersten freistehenden CVD-Blanks des US-amerikanischen Unternehmens Norton sah, erkannte ich sofort das Potenzial dieses Schneidstoffs. Am Anfang meiner Selbständigkeit half ich Norton diese Produkte als offizieller Händler für Europa zu vermarkten.“ so Dümpert. Sogar der Name Polydress (heute Ceradress) für CVD Abrichtstäbchen unter dem dann auch Norton weltweit vermarktete, wurde von ihm kreiert. Schließlich erhielt er aufgrund der erfolgreichen Vermarktung im März 1998 während einer Produktvorstellung für ca. 20 Werkzeughersteller sogar den Norton-Pioneers-Award.
„Als der Schleifmittelhersteller Norton nach der Jahrtausendwende – aus bis heute unbekannten Gründen – die Produktion von CVD-Diamant einstellte und selbst bestehende Aufträge nicht mehr ausliefern konnte, hatten wir die große Herausforderung, unsere Kunden weiterhin beliefern zu können“, gibt Reiner Dümpert zu verstehen. Doch Aufgeben war für ihn keine Option. „Ich stand vor einer großen Aufgabe: Wir konnten zwar nach einiger Zeit einen neuen Lieferanten (SP3, USA) ausfindig machen aber für eine rasche Lieferung von Zuschnitten an unsere Kunden mussten wir eigenständig unsere Kapazitäten, insbesondere für das Zuschneiden der Abrichtstäbchen ausbauen.“, so der 62-jährige.
„Wir haben uns schon immer in die Bedarfsstruktur unserer Kunden hineingedacht und haben daraus relevante Innovationen im Bereich der superharten Schneidstoffe und die hierfür erforderlichen Prozesse für den Werkzeugmarkt nach vorne gebracht. Schon 1997 wurden neue Diamantmaterialien, wie Ceraton CVD bzw. Ceradress CVD oder die Laser und schließlich auch die Vakuumlöttechnologie in der „Kreativwerkstatt“ Ceratonia angestoßen und mit Partnern umgesetzt.“
Reiner Dümpert
Bei Herstellern von Zerspanungswerkzeugen bremste folgende Situation die Akzeptanz des neuen Ceraton CVD Schneidstoffs: Es fehlte zum einen die Vakuumlötmöglichkeit und zum anderen die Lasertechnologie für die nachfolgende Bearbeitung der nicht erosiv bearbeitbaren 100%igen Diamantschicht. In Deutschland waren zunächst nur wenige Werkzeughersteller von Zerspanungswerkzeugen in der Lage, Schneidstoffe ohne HM-Träger im Vakuum zu löten. Andere behalfen sich bei externen Dienstleistern wie z. B. den Firmen Brütsch und Wabawaska. Die Schneidkanten von Ceraton CVD wurden bis dahin bei Natur,- und monokristallinen Diamanten nur durch einen aufwendigen Schleifprozess mit Diamantscheiben bearbeitet.
„Die sog. Global Player der Zerspanungswerkzeugindustrie wären wahrscheinlich schon in der Lage gewesen, die erforderlichen Investitionen zu tätigen, aber sie behandelten diesen, für alle neuen Markt, von Anbeginn stiefmütterlich. Das war bis dato die Domäne der klassischen Diamantwerkzeughersteller. Die Verwendung von Diamantschneidstoffen war für die „Großen“ offensichtlich eher eine Reduzierung ihres Umsatzes an HM-Werkzeugen – also war auch vor über 20 Jahren das neue Ceraton CVD nicht allzu interessant, wie Jahre zuvor schon das klassische PKD. Die Hersteller von Werkzeugen, die ausschließlich mit Diamant bestücken erkannten jedoch „im Besseren den Feind des Guten“ und waren bereit für diese Innovation bei den polykristallinen Schneidstoffen“ so bringt es Reiner Dümpert auf den Punkt.
Eine weitere Pionierleistung von Ceratonia bestand darin, die Möglichkeiten für die Bearbeitung seines CVD-Schneidstoffs bei potenziellen Kunden zu unterstützen: „Der Dreh- und Angelpunkt war und ist immer noch dabei die passende Laserbearbeitung. Die Lasertechnologie steckte damals noch in den Kinderschuhen. Im Herbst 1998 stellte Ceratonia den Werkzeugherstellern in Würzburg den ersten hierfür tauglichen Laser – damals von Laserpluss – vor. Dieser konnte zwar nur Zuschnitte aus den 26,2 x 26,2mm CVD-Blanks heraustrennen, aber es war die Geburtsstunde für die nun folgenden Jahre der Entwicklung geeigneter Anlagen“, gibt der studierte Maschinenbauingenieur zu verstehen. Ceratonia hat diesen Stein in’s Rollen gebracht und in Folge haben mehrere Hersteller von Maschinen zur Werkzeugfertigung ihre Laseranlagen weiterentwickelt. (z. B. Agathon, DMG, Ewag, Laserpluss Services, Rollomatic).
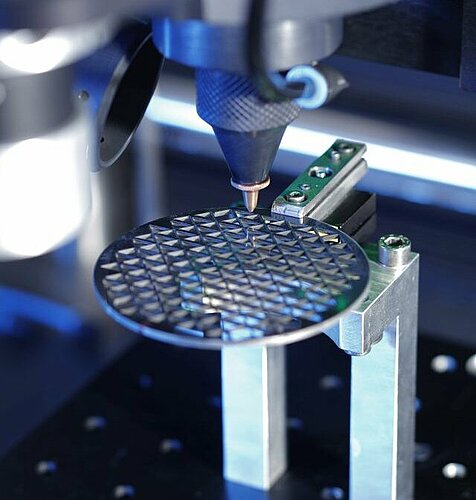
Unter dem Begriff „CVD“ verstand die Fachwelt der Werkzeughersteller damals nur eine dünne Beschichtung von Hartmetall. Der maßgebliche Unterscheid zu den damals gehypten Werkzeugschichten: Bei der CVD-Dickschicht handelt es sich um eine sogenannte freistehende Schicht größer 300µ, die auf das Werkzeug im Vakuum aufgelötet wird.
Im Industrie-Arbeitskreis (beteiligte Firmen: Riemke, Kieninger Technologie, Mössner, Laserpluss, Ceratonia) wurde das Thema der Laserbearbeitung von CVD-Dickschicht-Diamant zusammen mit dem IWF der TU Berlin von Anfang an aufgearbeitet und begleitet. Laserpluss lieferte dafür eine Anlage an die TU, Ceratonia den CVD Schneidstoff. Somit konnten die Fachkräfte des Instituts die Bearbeitungsprozesse optimieren und schon bald fantastische Ergebnisse vorweisen. Vor allem entwickelte Dümpert bei Ceratonia und dem Industrie-Arbeitskreis Strategien, um erst einmal präzise Zuschnitte aus den Basisplatten zu erzeugen. In einem zweiten Schritt begannen dann die Werkzeughersteller die Schneidkanten mit Laser zu bearbeiten und auch Spanleitstufen einzubringen. Die erzielbare Kantenschartigkeit übertraf schließlich die einer geschliffenen Schneidkante. Dann musste die Prozesswiederholbarkeit entwickelt werden.
Die „Löttechnologie“ für CVD haben die Werkzeughersteller eher aus dem Lötprozess für die Nischenprodukte Naturdiamant und MKD entliehen. Wenige Firmen hatten vor 20 Jahren schon Erfahrungen mit dem hierzu erforderlichen Vakuumlöten. Der gesamte Prozess war zum damaligen Zeitpunkt allerdings noch wenig durchleuchtet. Dümpert diente mit Dr. Flécher als Berater der Firma Wigtec und finanzierte die Produktion der ersten beiden Prototypen der neu entwickelten Vakuum-Lötanlagen. Findig war der gebürtige Unterfranke auch, als es darum ging, das heute einschlägige, moderne aber unabhängige, Branchenmagazin auf den Weg zu bringen. Dieses sollte für alle Lieferanten und Autoren zugänglich sein.
So berichtete das Fachmagazin Diamond Business 2002 erstmalig für die Branche über den neuen Schneidstoff CVD. Es unterstützte auch dessen Akzeptanz im Markt und weckte das Interesse bei Anwendern, die sich noch bessere Standzeiten als die mit PKD wünschten.
Steiniger Weg
Nach mittlerweile 25 Jahren lässt sich feststellen, dass sich der Schneidstoff Ceraton CVD und die Abrichtstäbchen sowie die Formplatten Ceradress CVD u. a. dank der Pionierarbeit von Dümpert in vielen Produktionsbereichen nicht mehr wegzudenken sind. Ein wichtiger Meilenstein der Firmengeschichte bestand im Fokus und Ausbau der Lasertechnik auch „inhouse“. Wie kein anderer Lieferant ist Ceratonia in der Lage, engste Toleranzen (+/-20μ) und kleinste Zuschnitte für Sonderanwendungen in Abmessungen von z. B. 0,2 x 0,2 x 0,7mm anzubieten. Dazu braucht es auch die Digitalmikroskopie (bis 2.000x), um die Produktion und auch feinste Körnungen zu messen und optisch zu kontrollieren. So entstand über die Jahre neben einer vielfältigen Auswahl an PKD- und CVD-Produkten ein umfangreiches Produktportfolio parallel zur Qualitätssicherung: Siebung der Diamant-, CBN-, und Natur-Körnungen bis hin zur Formsortierung nach Kundenwunsch.
Die Selbständigkeit von Dümpert entstand eher aus der Konsequenz heraus. Die Entlassungswelle im Jahre 1995 bei General Electric traf auch ihn. Dort war er seit 1989 als Betreuer der Schlüsselkunden für Nord- und später Mitteldeutschland tätig. So begann seine „Laufbahn“ in der Diamant- und CBN-Rohstoff-Branche als Zulieferer für die Werkzeughersteller der definierten Schneide- als auch die Säge-, Schleif-Werkzeugindustrie.
Reiner Dümpert erinnert sich gut: „Sehr schnell entwickelte ich eine Passion für Industriediamanten bzw. Superabrasives. Schon vor der Geburtsstunde von Ceratonia im Juni 1996 sinnierte ich im Dachstudio meiner Eltern am Schreibtisch des Vaters Lorenz immer wieder, wie ich meine gesammelten Erfahrungen und mein Wissen für die Branche zielführend und sinnbringend umsetzen könnte“. Schließlich recherchierte er oft bis in die Nachtstunden im Internet nach persönlich oder namentlich bekannten Firmen. Tagsüber kontaktierte er die Unternehmen und am späten Nachmittag, so gibt er zu verstehen, nutzte er häufig das Fahrrad für den Transport der einst noch wenigen Päckchen zur Post.
Mitglied im Supply Chain
„Wir müssen uns bei unserer Arbeit immer vor Augen halten, dass wir als Rohstoff- und Werkzeuglieferant in den Workflow des Kunden eingebunden sind und unser Team deshalb absolut zuverlässig agieren muss. Das heißt: Termine einhalten, die Ware in der gewünschten konstanten Qualität und Stückzahl fertigen bzw. bevorraten und stets reproduzierbar liefern. Die Werkzeuge unserer Kunden müssen auf der Maschine immer wieder das leisten, was vorgegeben und qualifiziert war. So gehört neben der Qualitätssicherung (ISO zertifiziert) zu unserem Prinzip, dass mindestens immer zwei Mitarbeiter mit jedem Prozess vertraut sind. So bleibt auch in Krankheits- oder Urlaubszeiten der Workflow stets erhalten.“
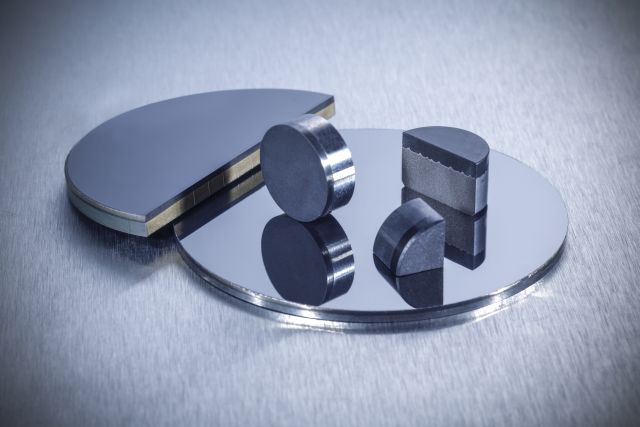
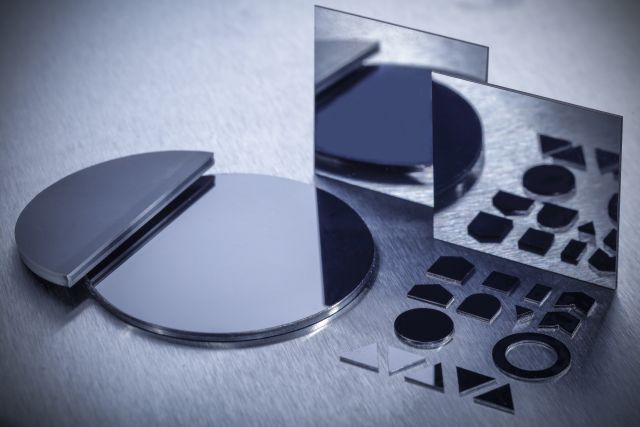
Nächste Generation am Start
Mit dem Zuwachs an Geschäftsbeziehungen ist Ceratonia stets gewachsen. Um 2000 hatte Dümpert bereits vier Mitarbeiter, weitere kamen stetig hinzu. Die Souterrain-Wohnung des Elternhauses hat er in ein Großraumbüro und den Keller in Technikräume umgestaltet, das Chefbüro blieb unter dem Dach. Die elterliche Wohnung war die Mittelschicht des Firmen-Sandwich. Der Alltag ein treppauf, treppab – unternehmerisch ging es trotz Untreue der Lieferanten und Verlusten von Mitarbeitern (auch zwei Mal an Marktbegleiter), steil nach oben! Aber wir konnten unseren Fachmann der Diamantbranche Bernd Hackel – ehemals bei Element Six beschäftigt – aus dem Ruhestand „reaktivieren“ und als top Unterstützer für unser Team gewinnen. Dieser suchte, wie er meinte: „einen Lieferanten als neuen Arbeitgeber der über gute Produktkenntnisse verfügt, diese Produkte im Portfolio hat und mit dem er auf Augenhöhe zusammenarbeiten kann“. Den fände er eben in Ceratonia.
Neben dem Beistand der Familie erfährt Dümpert beste Unterstützung durch Nachwuchskräfte im internationalen Vertrieb. So nennt er freudig „Ziehsohn“ Christopher Löhner in der Beratung der internationalen Kunden und Lisa Schnös, die ihn dabei tatkräftig unterstützt. Stellvertretend für das weitere Team nennt er seine „Säulen“ – die linken und rechten Hände: vier Mal Lisa und Sophia. Eine hat als Azubi bei Ceratonia begonnen und gehört heute zu seinen „Top Mädels“, erzählt er ganz stolz. „Auf unser Team kann ich mich verlassen. Ab 2012 gab es räumlich keine Alternative für den weiteren Ausbau. Wir platzten aus allen Nähten und brauchten ein auch für internationale Kunden repräsentatives Firmengebäude“, erinnert sich Dümpert. Anfang des Jahres 2014 zog Ceratonia nach Ebelsbach – etwa zwei Kilometer Luftlinie – in über 500qm Bürofläche.
Auch privat auf „Expansionskurs“
Seine drei erwachsenen Kinder haben mittlerweile ihren Platz in der Firma gefunden, freut sich Reiner Dümpert. Es scheint auch für Adrian (22), Gianna-Maria (21) und Laurence (18) zu gelten: Wer einmal im Diamantgeschäft gearbeitet hat, kommt davon schlecht wieder los. So hat schon jeder seinen Aufgabenschwerpunkt und wird bei den wesentlichen Entscheidungen ebenso wie die Mitarbeiter mit einbezogen. "So konnte Adrian bereits wesentliche Aufgaben bei der Markteinführung der Ceradite PKD Ronde in 62mm Durchmesser übernehmen, wo seine Kollegin Sabine Zenglein im Vertriebsinnendienst nichts anbrennen lässt. Gianna-Maria lernt jetzt die Produkte in der Abteilung Qualitätssicherung von der Pike auf Kennen. Und Laurence optimiert bzw. programmiert gemeinsam mit Patrick und Christoph die Laseranlagen und unterstützt Projekte der Produktqualifizierung." erklärt der mittelständige Geschäftsführer und Vater.
Reiner Dümpert hatte schon immer die Vision, mit seinen Produkten an erster Stelle zu stehen, wenn es um Werkzeugherstellung bzw. um die industrielle Nutzung von Diamant und CBN geht: „Wir sind erfreulicherweise nicht gezwungen nur das anzubieten, was eine Produktion von Körnung aus Diamant hervorbringt, sondern arbeiten mit verschiedenen Herstellern – den Marktführern der jeweiligen Produkttypen – als freier unabhängiger Händler zusammen. Dies gilt nicht zuletzt deswegen, weil wir vor über 10 Jahren nicht die besten Erfahrungen mit der Loyalität einiger Rohstoffhersteller machten. Daher qualifizierten wir in den nun 25 Jahren die besten Produkte aus den jeweiligen Produktionen (auch bei Naturdiamant) und vermarkten diese wie kaum ein anderer Lieferant in diesem Umfang unter unseren eigenen Produktnamen. Mit einem offenen Ohr am Markt, exklusiv für Diamant und CBN, sondieren, kategorisieren und prüfen wir die Qualität bestehender Produkte und neuer Hersteller im Sinne unserer Kunden. Angefangen beim Mikronpulver über alle Korngrößen hinweg, bis hin zu den polykristallinen Schneidstoffen CVD/PKD als auch bei der Aufbereitung von Naturdiamant sehen wir unsere Funktion als zuverlässiger Partner in Europa vor Ort. Ein Partner, der die Qualität der Schneidstoffe und auch die Lieferkette gerade in dieser unsicheren Zeit der weltweiten Pandemie als Rohstofflieferant sichert.“
Für den Erfolg von Ceratonia und für die ständige Weiterentwicklung sieht Reiner Dümpert auch ganz klar seine Mitarbeiter in Verantwortung. „Nur durch meine Mitarbeiter, deren Identifikation, Motivation und gelebten Teamgeist wurde und ist all dies möglich. Ich sehe in mir das brennende Feuer, das die anderen entfachen müssen. Dabei denke ich auch an all jene, die mittlerweile anderweitig ihre Ziele weiterverfolgen. Gerade heute in diesen unplanbaren und auch schwierigen Zeiten, ist es wunderbar ein starkes Team im Hintergrund zu wissen. Wie wir immer miteinander statt gegeneinander im Team und mit Kunden und Lieferanten zusammenarbeiten: das muss für alle heute und morgen passen. Entscheidungen haben bei uns kurze Wege, werden aber gut überlegt. Für strategische oder fachliche Fehler müsste ich und nun die Jungen im inhabergeführten Unternehmen immer persönlich und finanziell geradestehen. Mein Know-how über Markt und Produkte gebe ich an meine Kinder und Mitarbeiter täglich weiter damit „Ceratonia-Bäumchen“ weiter Wurzeln schlagen und Früchte tragen dürfen.“
Ein Wort zum Schluss
„Seit vielen Jahren fertigen übrigens alle namhaften Hersteller mit Synthesen vorwiegend in Asien. Wir kooperieren teilweise mit Produkten aus den gleichen Produktionen, wie die einstigen drei Global Player der „guten alten Zeit“. Wir lassen für uns nach eigenen Vorgaben konfektionieren. Entgegen der Anbieter aus „Fernost“, wie man die chinesischen Anbieter oft verschleiert gerne nennt, sehen wir uns „on Top“ auch immer wieder als Engineering-Partner und Anbieter zugeschnittener Lösungen statt nur, wie manche Marktbegleiter, die lediglich als Händler fungieren.“ so Dümpert abschließend.
VITA
Der Ingenieur Dümpert ist Jahrgang ´59 und hat an der Fachhochschule Schweinfurt den Studiengang Maschinenbau in Fachrichtung Konstruktion und Entwicklung absolviert. Seine erste Anstellung fand er in der Exportabteilung des Wälzlagerriesen FAG Kugelfischer (heute Schäffler) in Erlangen. Von 1986 bis 1988 baute er im Staat Connecticut, USA ein Tochterunternehmen für den Vertrieb und die Wartung von hydraulischen Rettungsscheren an Feuerwehren auf. „Das war eigentlich schon der erste Schritt in die Selbständigkeit, denn mein Part war damals schon ein Start als One-Man-Show. Ich fand dort ein leeres Lager, drei Büros, einen Dienstwagen und eine Lagerhalle vor. Vier Mitarbeiter kamen schnell dazu. Dies wiederholte sich dann quasi, denn der zwingende Ausbau aller Räume bis in den Keller im Haus meiner Eltern begleitete das stetige Wachstum im Umsatz als auch personell.“ beschreibt er schmunzelnd. Geprägt durch den Aufenthalt in USA, nennt er seine Mitarbeiter alle beim Vornamen und erwähnt, dass dies auch zu einem sehr guten Miteinander und einem persönlichen und verbindlichen „Corporate Behaviour“ und der echten Teambildung beitrage. Als er 1996 anfing, war er ganz „selbst-und-ständig“ für alle betrieblichen Belange zuständig: Vom Kundenbesuch, Pakete packen, Qualitätsprüfung, Einkauf, Buchhaltung bis zur EDV. Heute ist er zum gefragten Mittelständler geworden und unterhält zahlreiche Geschäftsbeziehungen in die ganze Welt.
Quelle | Ceratonia