Nachbearbeitung additiv gefertigter Titan-Bauteile mit höchster Präzision
Die Additive Fertigung ermöglicht die Herstellung hochkomplexer metallischer Bauteile mit höchster geometrischer Flexibilität in Leichtbauweise.
Darüber hinaus können zusätzliche Funktionalitäten wie Kühl- oder Medienkanäle direkt in die additiv gefertigten Bauteile integriert werden. Additive Fertigungsverfahren werden bereits heute erfolgreich in der Medizin- und Dentaltechnik, der Luft- und Raumfahrttechnik, im Automotivebereich sowie in der Elektronikbranche eingesetzt [1]. Bei der additiven Fertigung werden die Bauteile schichtweise aufgebaut, wodurch annähernd beliebig komplexe Geometrien, Hinterschneidungen sowie Strukturelemente fertigbar sind. Limitiert sind die verfügbaren Fertigungsverfahren hinsichtlich der herstellbaren Oberflächenrauheiten im Bereich von 5µm ≤ Ra ≤ 15µm, der Formgenauigkeiten von GF ≤ 1mm und des entstehenden Eigenspannungszustandes.
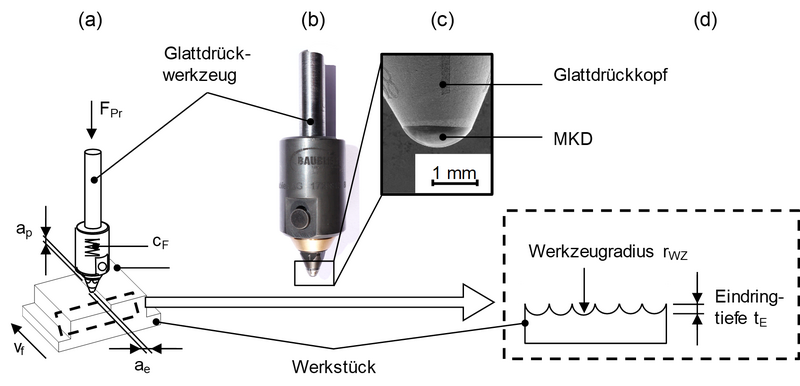
Die Herstellung additiv gefertigter Bauteile ist verfahrensbedingt durch Zugeigenspannungen σE geprägt, welche bei der Nachbearbeitung frei werden und in einem erheblichen Bauteilverzug resultieren. Zum aktuellen Stand der Technik existiert kein etabliertes Nachbearbeitungsverfahren, welches die Form, die Oberflächenrauheit und den Eigenspannungszustand applikationsgerecht adressiert. Gleichzeitig wachsen mit den technischen Möglichkeiten die Anforderungen an den Prozess und das Werkstück, wodurch stetig neue Anwendungsbereiche erschlossen werden und innovative Prozessketten notwendig sind.
Für metallische Bauteile, an welche besonders hohe Anforderungen bzgl. der Oberflächenrauheiten und Formgenauigkeiten GF gestellt werden, haben sich vor allem pulverbettbasierte Verfahren wie das Laser Powder Bed Fusion (L-PBF) etabliert. Mit diesem Verfahren können unter anderem Titan-Aluminium-Legierungen verarbeitet werden, welche aufgrund der spezifischen Werkstoffeigenschaften in der Luftfahrtindustrie und auf Basis der hohen Bioverträglichkeit Anwendung in der Medizintechnik finden [2, 3]. Nach aktuellem Stand der Technik werden die Erhöhung der Formgenauigkeiten GF sowie die Reduzierung der Oberflächenrauheitskennwerte von additiv gefertigten Bauteilen durch spanende und abtragende Verfahren realisiert [4]. Diese Verfahren basieren auf einem Trennvorgang, bei welchem die benannten Eigenspannungen σ frei werden und in einem Bauteilverzug resultieren. Eine Möglichkeit zur hochpräzisen Nachbearbeitung additiv gefertigter Bauteile besteht in der Entwicklung dedizierter Technologien zum Glattdrücken. Das übergeordnete Entwicklungsziel ist die Bereitstellung einer prozesssicheren Technologie zum hochpräzisen Glattdrücken von additiv gefertigten Funktionsbauteilen.
Verfahrensprinzip des Glattdrückens
Das Glattdrücken auf Fräsmaschinen ist ein noch relativ unbekanntes Verfahrensprinzip und schematisch in Abbildung 1a dargestellt. Das modulare Glattdrückwerkzeug der Firma Baublies AG, Renningen Malmsheim, welches in Abbildung 1b dargestellt ist, setzt sich aus einem Werkzeughalter, einer Feder mit einer Federkonstanten cF und einem Glattdrückkopf (s. Abb 1c) mit einem sphärisch ausgeprägten fixierten monokristallinen Diamanten (MKD) zusammen. Zur Anwendung des Glattdrückens wird der Glattdrückkopf in die Oberfläche des zu bearbeitenden Bauteils eingedrückt und dieses mit einer entsprechenden Bearbeitungsstrategie, einer definierten Vorschubgeschwindigkeit vf sowie einer definierten Prozesskraft FPr nachbearbeitet. Die Prozesskraft FPr wird in Abhängigkeit der axialen Zustellung ap sowie der eingesetzten Feder mit der Federkonstanten cF eingestellt. Das Glattdrücken stellt somit einen Druckumformprozess nach DIN 8583 5 [5] dar. Dabei werden Druckeigenspannungen σD induziert, wodurch nachbearbeitungsbedingter Bauteilverzug reduziert und eine Erhöhung der Formgenauigkeiten GF sowie Reduzierung der Oberflächenrauheiten erzielt werden können. Zudem erfolgt eine Steigerung der Härte H in Abhängigkeit der Prozessparameter. Eine schematische Darstellung der geometrischen Verhältnisse ist in Abbildung 1d dargestellt.
Präzisionsnachbearbeitung - Versuchsaufbau
Die technologischen Entwicklungen zur Präzisionsnachbearbeitung durch das Glattdrücken erfolgten auf der 5 Achs Hochpräzisions Fräsmaschine HSC MP7/5 der Firma Exeron GmbH, Oberndorf. Basierend auf den zum Stand der Technik beschriebenen Herausforderungen wurden Entwicklungen zur Präzisionsnachbearbeitung additiv gefertigter Bauteile aus der Ti-Al-Legierung des Typs 5553 durchgeführt. Zur Herstellung der additiv gefertigten Bauteile ist das Verfahren Laser Powder Bed Fusion verwendet worden. Als Basis für die technologischen Entwicklungen dienten die bereits beschriebenen Glattdrückwerkzeuge der Baublies AG, Renningen-Malmsheim, welche über eine Feder mit der Federkonstanten cF = 34,4 N/mm zur Prozesskrafteinstellung sowie einen Glattdrückkopf aus MKD mit einem Werkzeugradius von rWZ = 2,0mm verfügen. Für die Versuchsdurchführungen wurden eine Vorschubgeschwindigkeit von vf = 1.000 1/min, eine Drehzahl von n = 0 1/min sowie eine mäanderförmige Bearbeitungsstrategie mit Minimalmengenschmierung verwendet. Damit die additiv gefertigten Bauteile verfahrensgerecht im Maschinenraum fixiert bzw. gespannt werden konnten, wurden die Versuchsproben im Vorfeld einseitig bearbeitet und eine spezielle Werkstückspannvorrichtung entwickelt. Für die messtechnische Erfassung der Oberflächenrauheitskennwerte und Formgenauigkeiten GF wurde das Rauheits- und Konturmessgerät vom Typ Hommel-Etamic nanoscan 855 der Firma Jenoptik AG, Jena, verwendet. Die Ermittlung der Prozesskräfte FPr wurde mit dem Dreikomponenten-Dynamometer des Typs 9265A der Firma Kistler Instrumente AG, Winterthur, Schweiz, umgesetzt.
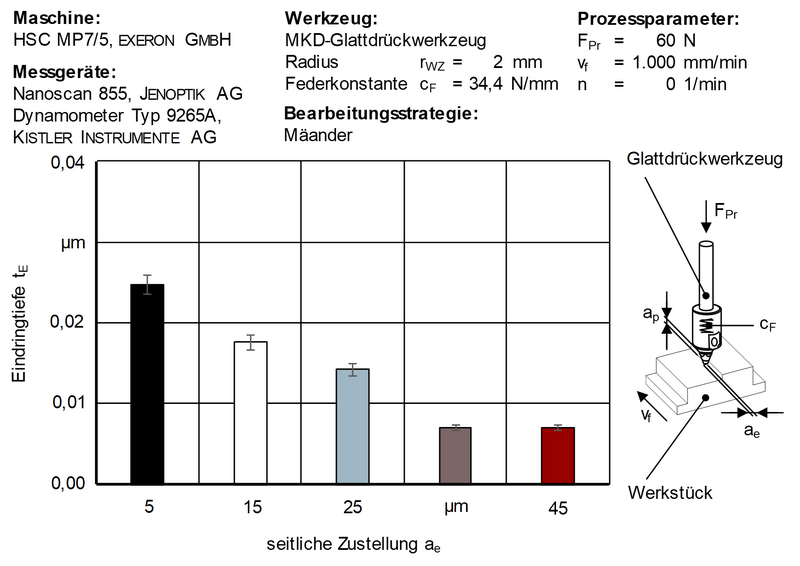
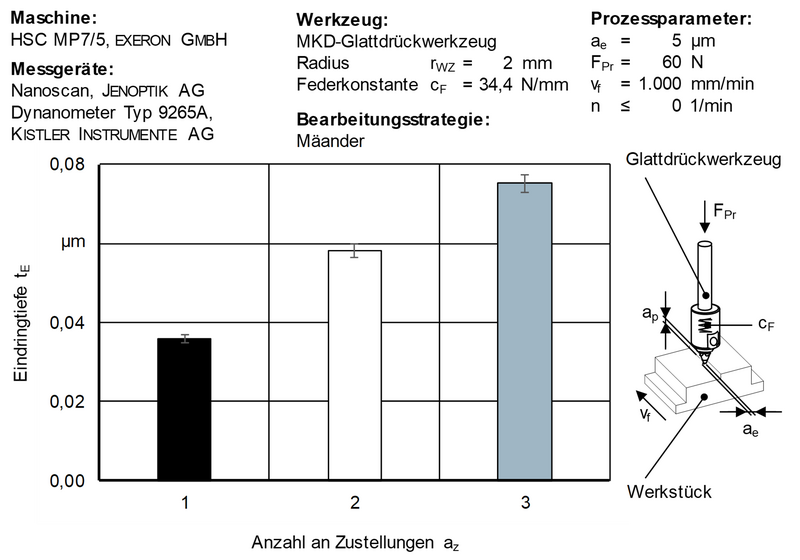
Formgenauigkeiten GF
Um eine präzise Nachbearbeitung mittels Glattdrücken zu ermöglichen, ist ein definiertes Einstellen der Prozesskraft FPr erforderlich. Dies erfolgt über die axiale Zustellung ap der sich eindrückenden Feder mit der Federkonstante cF = 34,4N/mm. Im Vorfeld dieser Untersuchungen wurde bereits die Abhängigkeit zwischen der Prozesskraft FPr und der axialen Zustellung ap sowie zwischen der Prozesskraft FPr und der Eindringtiefe tE ermittelt. Die Ergebnisse zeigten, dass sowohl die Prozesskraft FPr in Abhängigkeit der axialen Zustellung ap als auch die Eindringtiefe tE in Abhängigkeit der Prozesskraft FPr definiert eingestellt werden können und eine Präzisionsnachbearbeitung von additiv gefertigten Bauteilen aus der Ti-Al-Legierung des Typs 5553 realisierbar ist [UHL20]. Demnach soll in weiterführenden Untersuchungen nun die Abhängigkeit zwischen der Endringtiefe tE und der seitlichen Zustellung ae sowie der Einfluss einer mehrmaligen Zustellung zur Herstellung hoher Formgenauigkeiten GF analysiert werden. Für die Untersuchungen zur Präzisionsnachbearbeitung wurde jeweils eine Prozesskraft FPr = 60N verwendet.
Die Analyse des Einflusses der seitlichen Zustellung ae auf die Eindringtiefe tE erfolgte mit fünf Variationsstufen in einem Bereich von 5µm ≤ ae ≤ 45µm. Die Arbeitsergebnisse sind in Abbildung 2 dargestellt. Dabei ist ersichtlich, dass sich die Eindringtiefe tE in Abhängigkeit der seitlichen Zustellung ae ändert und unter Einhaltung einer Formgenauigkeit GF ≤ 5µm definiert eingestellt werden kann. Darüber hinaus wird ersichtlich, dass mit einer steigenden seitlichen Zustellung bis zu einem Wert von ae = 35µm die Eindringtiefe tE annähernd linear abnimmt und bei einem Wert von ae ≥ 45µm sich eine Eindringtiefe von tE = 7µm einstellt. Dies ist auf die geänderten Eingriffsbedingungen und die Abhängigkeit zum Werkzeugradius rw des eingesetzten Glattdrückwerkzeugs zurückzuführen. Bei einer Vergrößerung der seitlichen Zustellung ae wird die Fläche A des zu verdrängenden Werkstoffs erhöht, wodurch bei gleichbleibender Krafteinwirkung die Flächenpressung pB reduziert wird und damit der Umformgrad φ sowie die Eindringtiefe tE abnimmt. Ergänzend dazu wurde der Einfluss einer wiederholten Zustellung auf die Eindringtiefe tE untersucht, um die Auswirkungen auf die Eindringtiefe tE und die erreichbare Formgenauigkeit GF bestimmen zu können (s. Abb. 3). Dazu wurde eine Bearbeitungsfläche AB unter Berücksichtigung einer dreimaligen Zustellung mit identischen Prozessparametern glattgedrückt und die einzelnen Eindringtiefen tE messtechnisch erfasst. Die Ergebnisse zeigen, dass in Abhängigkeit der Anzahl der Zustellungen az die Eindringtiefe tE präzise erhöht werden kann, der Anstieg jedoch kontinuierlich abnimmt. Dies ist dabei auf werkstofftechnische Aspekte bei der kontinuierlichen Umformung der Ti-Al-Legierung zurückzuführen. Weiterhin ist erkennbar, dass die Ausgangsfläche AA von übergeordneter Bedeutung für das Prozessergebnis ist.
Oberflächenrauheiten
Neben dem Nachweis der Präzisionsnachbearbeitung unter Einhaltung einer Formgenauigkeit von GF ≤ 5µm steht die Realisierung geringer Oberflächenrauheiten von Ra ≤ 200nm im Fokus der Untersuchungen. Für die detaillierte Analyse der Auswirkungen des Glattdrückprozesses auf die Oberflächenrauheiten wurde der Einfluss der Prozesskraft FPr sowie der seitlichen Zustellung ae untersucht. Im Ausgangszustand wies das Werkstück einen arithmetischen Mittenrauwert von Ra = 8,34µm auf. In den nachfolgend dargestellten Untersuchungen wurde ein Prozesskraftbereich von 40N ≤ FPr ≤ 120N angewandt. Die Abbildung 4 stellt den arithmetischen Mittenrauwert im Bereich von 0,183µm ≤ Ra ≤ 0,930µm in Abhängigkeit der eingesetzten Prozesskräfte FPr dar. Die Ergebnisse zeigen steigende arithmetische Mittenrauwerte Ra bei einer Erhöhung der Prozesskraft FPr. Für eine Prozesskraft von FPr = 40N zeigt sich, dass dabei insbesondere die für einen dedizierten Umformprozess notwendige Flächenpressung pB nicht erreicht ist und der arithmetische Mittenrauwert lediglich auf Ra = 0,93µm reduziert werden konnte.
Bei einer Prozesskraft von FPr ≥ 80N wird mehr Werkstoff plastisch verdrängt als erforderlich ist, um eine definierte Oberflächenstruktur zu erzeugen. Das überschüssige plastisch verdrängte Werkstoffvolumen VW wird dabei neben dem Glattdrückwerkzeug aufgeworfen. Der geringste arithmetische Mittenrauwert von Ra = 0,186µm konnte bei einer Prozesskraft FPr = 60N nachgewiesen werden. Auf Basis dieser Untersuchungen ist eine Reduzierung des arithmetischen Mittenrauwerts Ra von ~ 98% im Vergleich zum Ausgangszustand nachgewiesen worden. Zur vollständigen Charakterisierung der wichtigsten Einflussgrößen beim Glattdrücken wird abschließend der Einfluss der seitlichen Zustellung ae auf den arithmetischen Mittenrauwert Ra analysiert. Für die Untersuchung wurde die seitliche Zustellung in einem Bereich von 5µm ≤ ae ≤ 45µm variiert. Der Einfluss der seitlichen Zustellung ae sowie die Ergebnisse der Untersuchungen sind in Abbildung 5 illustriert. Aus der Erhöhung der seitlichen Zustellung ae resultiert ein gleichmäßiger Anstieg des arithmetischen Mittenrauwerts Ra bis zu einem Wert von ae ≤ 35µm.
Dieser Effekt kann auf die Erhöhung der theoretischen Rautiefe Rth aufgrund der Eingriffsverhältnisse und der Werkzeuggeometrie zurückgeführt werden. Ab einer seitlichen Zustellung von ae ≥ 35µm kommt es nur noch zu einem minimalen Anstieg des arithmetischen Mittenrauwerts Ra. Die nur noch minimale Änderung des arithmetischen Mittenrauwerts Ra ab einer seitlichen Zustellung von ae ≥ 35µm ist auf Basis der Ergebnisse in Abbildung 2 begründbar, da sich hierbei die Eindringtiefe tE bzw. der Umformgrad φ in Abhängigkeit einer definierten Prozesskraft FPr und des eingesetzten Glattdrückwerkzeugs nicht mehr signifikant ändert. Demzufolge verringert sich dabei die theoretische Rautiefe Rth. Der geringste arithmetische Mittenrauwert von Ra = 0,175µm konnte bei einer seitlichen Zustellung von ae = 5µm nachgewiesen werden, was mit den Ergebnissen aus Abbildung 4 vergleichbar ist. Zusammenfassend zeigen die Ergebnisse, dass eine präzise Nachbearbeitung additiv gefertigter Bauteile unter Einhaltung eines arithmetischen Mittenrauwerts von Ra ≤ 200nm in Abhängigkeit der Prozesskraft FPr und der seitlichen Zustellung ae realisierbar ist. Damit kann die entwickelte Prozesskette zur Herstellung hochpräziser additiv gefertigter Bauteile unter Einhaltung einer Formgenauigkeit von GF ≤ 5µm und eines arithmetischen Mittenrauwerts von Ra ≤ 200nm um wichtige wissenschaftliche Erkenntnisse erweitert werden. Zur Visualisierung der erreichbaren Bauteilqualität ist in Abbildung 6 ein exemplarisches Bauteil dargestellt.
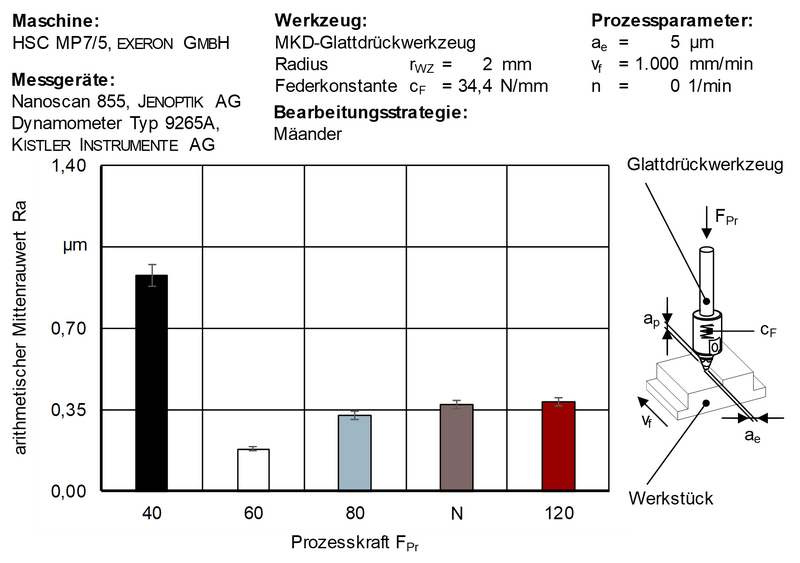
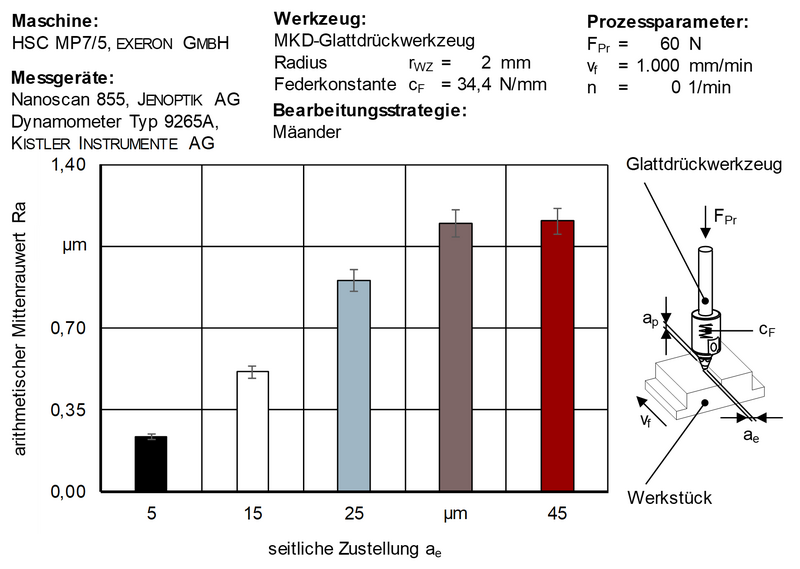
Ergebnisse und Ausblick
Das übergeordnete Ziel der Untersuchungen war die Bereitstellung einer prozesssicheren Technologie zum hochpräzisen Glattdrücken von additiv gefertigten Funktionsbauteilen aus Titan. Aufbauend auf bereits durchgeführten Vorentwicklungen wurden die Zusammenhänge zwischen der Eindringtiefe tE und der seitlichen Zustellung ae sowie wiederholter Zustellvorgänge analysiert. Es konnte gezeigt werden, dass sowohl mit der Variation der seitlichen Zustellung ae als auch mit wiederholtem Zustellen eine Präzisionsnachbearbeitung additiv gefertigter Bauteile realisierbar ist. Zum Abschluss der Untersuchungen wurden die Auswirkungen der Prozesskraft FPr und der seitlichen Zustellung ae auf die Entstehung der Oberflächenrauheiten analysiert.
Es konnte nachgewiesen werden, dass sowohl die Prozesskraft FPr als auch die seitliche Zustellung ae einen wesentlichen Einfluss auf die Entstehung der Oberflächenrauheiten aufweisen. Den Ergebnissen ist weiterhin zu entnehmen, dass für eine präzise Umformung die werkstoffspezifische Flächenpressung pB einen entscheidenden Einfluss ausübt. Diese ist vom Werkstoff und den Prozessgrößen wie der seitlichen Zustellung ae und der Prozesskraft FPr abhängig und ist für für die hochpräzise Nachbearbeitung von additiv gefertigten Bauteilen zu berücksichtigen. Auf Basis der Untersuchungen ist es möglich, Funktionsbauteile aus der Ti-Al-Legierung des Typs 5553 in einer additiven Prozesskette hochpräzise mit Formgenauigkeit GF ≤ 5µm und arithmetischen Mittenrauwerts Ra ≤ 200nm zu fertigen.
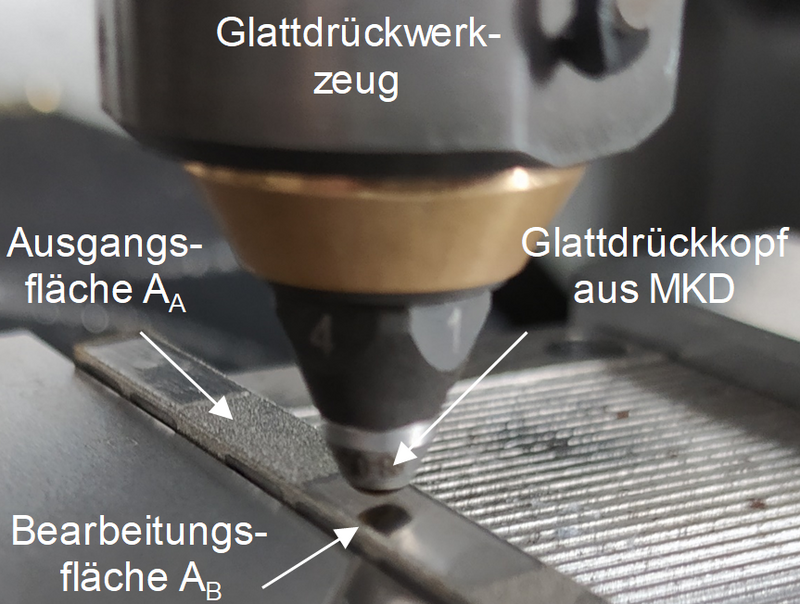
Literaturhinweis
[1] Gausemeier, J.; Echterhoff, N.; Kokoschka, M.; Wall, M.: Thinking ahead the Future of Additive Manufacturing – Analysis of Promising Industries. Paderborn: Universität Paderborn, Heinz-Nixdorf-Institut, DMRC, 2011.
[2] Leach, R. K.; Bourell, D.; Carmignato, S.; Donmez, A.; Senin, N.; Dewulf, W.: Geometrical metrology for metal additive manufacturing. CIRP Annals 68 (2019) 2, S. 677 – 700.
[3] Manfredi, D.; Calignano, F.: Laser powder bed fusion of aluminum, titanium and nickel based alloys: Materials and design investigations. In: International Conference on Electromagnetics in Advanced Applications (ICEAA) IEEE, 2017,
S. 1.423 – 1.425.
[4] Kumbhar, N. N.; Mulay, A. V.: Post Processing Methods used to Improve Surface Finish of Products which are Manufactured by Additive Manufacturing Technologies: A Review. J. Inst. Eng. India Ser. C 99 (2018) 4, S. 481 – 487.
[5] DIN 8583-5, Teil 5, (09.2003) Fertigungsverfahren Druckumformen; Eindrücken; Einordnung, Unterteilung, Begriffe. Berlin: Beuth.
[6] Uhlmann, E.; Polte, J.; Hocke, T.; Lahoda, C.; Siebel, D.: Präzisionsnachbearbeitung additiv gefertigter Bauteile im Mikrometerbereich. MM Maschinenmarkt (2020).
Quelle | TU Berlin