Transparente Schleifprozesse mittels Prozessmonitoring
Das Schleifen wird gemäß der DIN8589 als „Bearbeitungsprozess mit geometrisch undefinierten Schneiden“ definiert.

Wälzschleifprozesses
Das mag an manchen Stellen zu der auch heute noch irrtümlichen Meinung führen, dass somit der Schleifprozess auch nicht genau definierbar sein kann. Dieser Aufsatz will dieser Definition entgegenwirken und zeigen, dass auch der komplexeste Schleifprozess, wie ihn das kontinuierliche Wälzschleifen von Verzahnungen darstellt, durchaus transparent und verständlich gemacht werden kann. Das hier vorgestellte Prozess-Überwachungssystem Argus macht den Schleifprozess transparent und analysierbar und kann Anwenderforderungen, wie zum Beispiel der Null-Fehler-Produktion, gerecht werden.
Einfach ausgedrückt, überwacht Argus die Abricht- und Schleifintensität mittels intelligenter Echtzeit-Datenverarbeitung und erprobten Algorithmen. Die Abricht- und Schleifprozessdaten eines jeden einzelnen Zahnrades werden aufgezeichnet, in einer Datenbank abgelegt und bleiben 100% rückverfolgbar. Mit Hilfe der ebenfalls gespeicherten Prozess- und Toolingdaten, sowie auch der Werkstückidentifikation (Data Matrix Code oder kurz DMC) ergeben sich umfassende Analysemöglichkeiten. Dank der Prozessinteraktion werden, unter Berücksichtigung eingestellter Bewertungsgrenzen, grenzüber- oder unterschreitende Werkstücke automatisch ausgeschleust.
Im Vortrag werden die nachfolgenden Elemente genauer dargestellt:
Schleifprozessüberwachung |
Abrichtprozessüberwachung |
Komponentenüberwachung |
Webbasierte Prozessansicht |
Datenaufzeichnung |
Kontinuierliches Wälzschleifen
Das kontinuierliche Wälzschleifen hat sich als das produktivste Verfahren der Hartfeinbearbeitung von hochgenauen Zahnrädern durchgesetzt. Abbildung 1 zeigt das Achskonzept und die Wälzschleifkinematik.
Schleifprozessüberwachung
Eines der wesentlichen Merkmale der Wälzschleifmaschine ist eine hohe Teileausbringung in kurzer Zeit. Somit können in der Regel nicht alle gefertigten Teile, ohne erheblichen Aufwand und damit verbundenen Kosten, taktil gemessen werden. Letztendlich beschränkt sich die Verzahnungsindustrie daher auf Stichprobenanalysen. Im Rahmen der genannt hohen Produktionsmenge, insbesondere bei den typischen Prozessen der Serienfertigungen im Automobilbereich, lassen sich wirtschaftliche Prüfungen aktuell nur im einstelligen Prozentbereich der Fertigungsmenge durchführen.
Generell gilt das kontinuierliche Wälzschleifen von Verzahnungen als sehr stabiler und robuster Prozess, der durch wiederkehrendes Abrichten und das schon erwähnte Schiften während der Bearbeitung nahezu gleichbleibend hohe Qualität garantiert. Unter dem wachsenden Qualitätsanspruch der Verzahnungsindustrie an die gefertigten Räder, werden nicht nur ständig neue Prüfmethoden etabliert, sondern auch die 100% Prüfung und Überwachung aller Prozesse gewinnt zunehmend an Bedeutung. Mit den heute typischen Stichprobenanalysen besteht das, wenn auch geringe Restrisiko, schlechte Werkstücke in ein Getriebe zu verbauen. Üblicherweise sind taktile Messmethoden auch nur bedingt geeignet, geräuschauffällige Räder infolge der meist sehr kleinen Oberflächenwelligkeiten zu identifizieren.
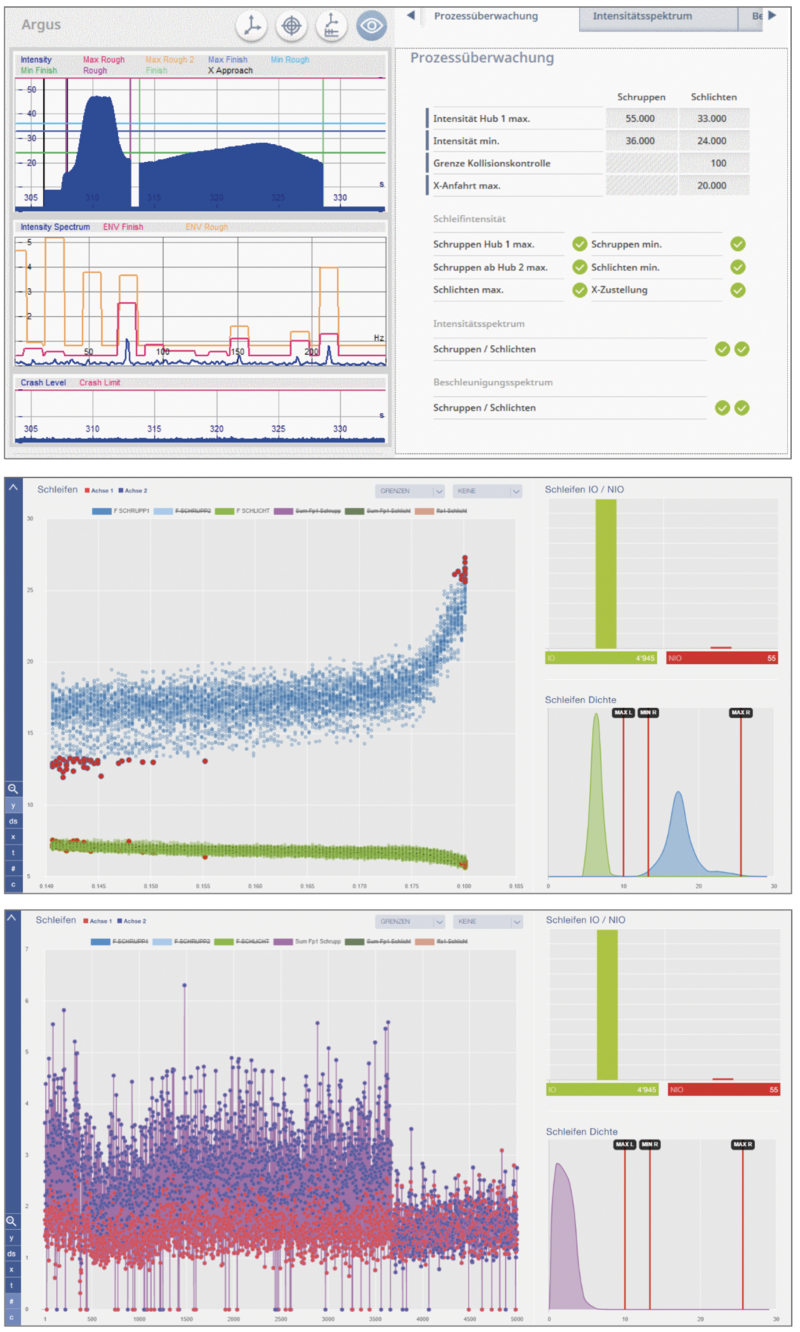
Dieses Restrisiko schlechte Werkstücke zu verbauen wird hingegen aufgehoben, wenn während der Bearbeitung die Schleifkraft, bzw. die Schleifintensität als Bewertungskriterium überwacht wird. Dank einer Echtzeitanalyse dieses Signals kann noch während des Schleifprozesses ein fehlerbehaftetes Werkstück, bei entsprechender Grenzwertverletzung, identifiziert werden. Mittels vorhandener Automatisierung der Fertigungskette, werden diese Ausschussteile automatisch aus dem Produktionsvorgang ausgeschleust. Danach produziert die Maschine weiter. Erst nach einer wiederholten Ausschleusung von Teilen erkennt die Anlage einen systematischen Fehler, stoppt den Betrieb und gibt dem Anwender eine Fehlermeldung aus.
Die Ursache von zum Beispiel grenzüber- oder unterschreitender Schleifintensität könnte zu viel oder zu wenig Schleifzugabe, zu hoher Härteverzug und die damit verbundene zu hohe Rundlaufabweichung sein. Auch mit Hilfe der Sensorik für die Vormessung, bzw. Rohteilprüfung, kann bereits auf Toleranzüberschreitungen reagiert werden. Zu hohe Rundlaufabweichungen oder Teilungsfehler führen entweder dazu, dass die Steuerung einen weiteren Zusatzhub automatisch unter Berücksichtigung der Hubaufteilung hinzufügt, oder zum direkten Ausschleusen des fehlerbehafteten Rohteils. Unter der Argus Schleifintensität versteht der Hersteller ein dem Prozess zugrundeliegendes Kraftmodell zur Normierung der Schleifkräfte.
Dieses Modell berücksichtigt unter anderem die Ausprägung der Spanungszone inklusive der lokalen Schnittkinematik bei Veränderung des Durchmessers der Schleifschnecke, die Veränderung der schleiftechnologischen Parameter wie beispielweise die Drehzahlen und die vorliegenden Hebelverhältnisse. Dank dieser Normierung ist es möglich, sehr enge Grenzen zur Bewertung des Prozesses zu setzen, woraus eine hohe Auflösung der Fehlerbewertung resultiert. Demnach können bereits kleine Kraftschwankungen durch unterschiedliche Aufmaße am Rohteil nicht nur erkannt, sondern vor allem automatisch bewertet werden. Ein typischer Intensitätsverlauf für eine zweistufige Bearbeitung ist in Abbildung 2 zu sehen. Aus der Schleifintensität wird auch ersichtlich, ob sich eine Schleifschnecke über ihren Durchmesser- und Breitenbereich konstant verhält oder nicht. Die Beurteilung von Schleifschnecken wird oft sehr subjektiv behandelt, da es meist an empirischen Werten fehlt und inhomogene Härteverläufe der Schleifschnecken nur indirekt über einbrechende Profilabweichungen der Werkstücke sichtbar werden, obwohl dies auch andere Ursachen haben könnte. Mit Argus wird eine Veränderung des Härteverlaufs einer Schleifschnecke messbar, sichtbar und referenzierbar gemacht, wie in Abbildung 3 zu sehen.
Abbildung 3 zeigt die Schleifintensitäten über der Position der Y-Achse bzw. entlang der Schneckenbreite bei ca. 5.300 Werkstücken, wobei die obere Punktewolke den Schrupphub darstellt und die untere engere Punktewolke den Schlichthub. Beim Schrupphub ist von rechts nach links ein Abfall in der Schleifintensität festzustellen, der sich in einer gegenläufigen Zunahme der Schleifintensität beim Schlichten spiegelt. Das Abfallen der Schrupp-Intensität deutet auf einen prozessbedingten Verschleiß am Schleifwerkzeug, also der Schleifschnecke, hin. Generell garantiert das verwendete Kraftmodell und die damit verbundene Normierung, einem nahezu konstanten Level der Schleifintensität entlang der Schneckenbreite und über den gesamten Bereich des Werkzeugdurchmessers. Das nun vorliegende abfallende Intensitätsniveau resultiert demzufolge ausschließlich durch eine aufbauende mikroskopische Zerstörung des Korngebindes der Schnecke, was zu einem geringeren Materielabtrag am Zahnrad führt. Die leichte Zunahme der Schleifintensität beim Schlichten deutet auf die resultierende Kompensation des Schlichthubes hin, wo letztendlich das nicht abgetragene Material der vorangegangenen Bearbeitungsstufe zusätzlich entfernt werden muss. Dieser beschriebene Effekt führte final auch zu zunehmend ausgeschleusten Teilen, die unten links in der Punktwolke des Schruppens als dunkelrote Punkte erscheinen.
Die Schleifintensität gibt unter anderem auch Einblick in die Rundlaufgenauigkeit der Spannmittel oder der Rundlaufabweichung der Vorbearbeitung. Die nachstehende Abbildung 4 zeigt die Rundlaufabweichung von beiden Werkstückspindeln C1 und C2, die sich im Drehturm der Schleifmaschine befinden. In der obigen Darstellung ist der Rundlaufindikator des Argus Systems visualisiert. Zur einfachen Interpretation solcher dynamischen Effekte berechnet das Argus System, unter Verwendung erprobter Algorithmen, automatisch den Anteil der in diesem Beispiel diskutierten Rundlaufabweichung aus den aufgenommenen Zeitsignalen der Messeinheit. Dank der Verwendung der Indikatoren entstehen mehrere signifikante Vorteile für den Anwender. Nebst der einfachen Interpretierbarkeit resultiert die Eigenschaft, dass Analysen des komplexen Verfahrens nun nicht mehr ausschließlich von teuren und hochausgebildeten Experten durchgeführt werden können, sondern auch die Möglichkeit der Visualisierung großer Fertigungslose. Während in akademischen Studien gerne auf Zeit- und Frequenzbereichsanalysen mit großen Datenmengen zurückgegriffen wird, die mehrere Gigabytes an Daten enthalten, lassen sich mit dem skalaren Format der Kennwerte problemlos tausende von Messpunkten aufzeigen. Zudem benötigt es auch keine besondere Auswertungssoft- und Hardware für damit verbundene Prozessanalysen, sodass eine einfache Webapplikation in typischen Browsern genutzt werden kann. Dank der kleinen Datenmenge können alle Daten auch jederzeit via Internet oder allgemeinem Netzwerk, auch mit kleiner Netzwerkbandbreite effizient geladen werden.
Die roten Punkte in der Abbildung 4 verdeutlichen eine konstant kleine Prognose zur Rundlaufabweichung bezüglich der C-Achse 1 über ca. 5.300 Werkstücke. Generell liegt hier auch eine typische geringe Streuung vor, die aus der Vorbearbeitungsqualität resultiert. Die blauen Punkte weisen im Verlauf von ca. 3/4 der Werkstücke eine höhere Abweichung im Rundlauf des Spannmittels der C2 Werkstückspindel auf, bis diese rundgerichtet wurde und der Prozess danach bei beiden Spindeln deckungsgleich verlief. Diese konstante Level-Erhöhung des Rundlaufs kann nur sich nur aus einer konstanten Eingangsgröße abbilden, was auf die Rundlaufabweichung des eingerichteten Spannmittels deutet, oder im Ausnahmefall auf eine konstante Unrundheit der Eingangswerkstücke schließen lässt. Letztere genannte Werkstückvorbearbeitung liefert jedoch meist eine starke Streuung des Rundheitsindikators und kann auch zu Ausschleusungen dieser Teile führen.
Unter vielen weiteren Eigenschaften von Argus soll hier die Wirtschaftlichkeit des Schleifprozesses angesprochen werden. Abgesehen von geometrischen Ungenauigkeiten nimmt der Schleifbrand eine wichtige Rolle in der Produktionssicherheit ein. Er muss unter allen Umständen vermieden werden und eine gängige Strategie ist es, auf Nummer Sicher zu gehen und die Vorschübe zurückzufahren, da die Schleifbrandgrenzen nicht bekannt sind. Wenn man die Schleifintensitäten entsprechend kalibriert und weiß, dass man brandfrei produziert, kann der brandfreie Schleifbereich mittels höheren Vorschüben und geringeren Shift-Werten wirtschaftlich optimiert werden, da man die Schleifzeit kürzen und die Standzeit der Schleifschnecke und der Diamantrollen erhöhen kann. Wie in der Einleitung erwähnt wurde, ist das Ziel der Schleifprozessüberwachung die Null-Fehler-Produktion.
Abrichtprozessüberwachung
Das Abrichten von Schleifscheiben ist für alle Schleifprozesse von höchster Bedeutung. Dies trifft auch auf den Wälzschleifprozess zu. Das rotierende Abrichtwerkzeug verleiht der Schleifschnecke ihr genaues Profil und auch ihre Schnittigkeit. Mittels der Wälzbewegung im Schleifen werden mit dem Schleifschneckenprofil die Evolventen und schließlich auch die gesamten Zahnflanken generiert. Jedweder Profilfehler des Diamantwerkzeuges spiegelt sich unmittelbar im Zahnflankenprofil. Ist das Diamantabrichtwerkzeug stumpf, wird die Schleifschnecke nicht die notwendige Schnittigkeit aufweisen, reduziert die Abtragsleistung und könnte Schleifbrand zu Folge haben.
Generell verfolgt Argus auch beim Prozessüberwachen des Abrichtens die Strategie der Indikatoren zur Beurteilung des Verfahrens. So gibt es im Argus abrichtbezogene technologische Indikatoren, die beispielsweise auf den Verschleiß der Diamantabrichtrolle deuten. Weist eine Schleifschnecke Bruchstellen in ihren Gängen auf, so führt dies generell zu Formabweichungen. Natürlich gibt es auch Indikatoren, die unter anderem aus dem Signal der Abrichtintensität berechnet werden und auf einen vorhandenen Bruch deuten. Die nachstehende Abbildung 5 zeigt, dass das Abrichtüberwachungsprogramm in der Lage ist, Schleifscheibenausbrüche zu detektieren. In diesem Falle wurden die Ausbruchstellen bewusst in die Schneckengänge eingeführt. Es wurden sechs Abrichtzyklen durchgeführt, die zeigen, wie die Ausbruchstellen sukzessive kleiner werden und beim letzten Zyklus ganz verschwunden sind. Bis anhin wurden Diamantabrichtwerkzeuge ausgetauscht, wenn eine bestimmte Anzahl von Werkstücken geschliffen wurde. Dies war oft unabhängig, ob das Abrichtwerkzeug noch weiterhin verwendet wurde oder nicht. Aufgrund der Abrichtintensität und der Indikatoren zum Diamantverschleiß kann der akzeptable Grenzwert der Abstumpfung bestimmt werden und das Abrichtwerkzeug kann bis zum effektiven Standzeitende ausgenutzt werden, was über Zeit zu beachtlichen Kosteneinsparungen führt.
Maschinenkomponenten-Überwachung
Das Argus Überwachungssystem verhindert unnötige Serviceeinsätze und damit verbundene Stillstandzeiten und Mehrkosten. Die Serviceeinsätze werden somit besser planbar und letztendlich kostengünstiger. Unter Berücksichtigung stabiler Bearbeitungsprozesse und entsprechender Vorbearbeitung, resultieren bei unbeschädigtem Komponentenzustand auch generell nur Werkstücke in gewünschter Qualität. Demzufolge trägt daher auch die Komponenten-überwachung einen signifikanten Teil zur Qualitätssicherung in der Fertigung bei. Spezifische NC Programme werden zyklisch aufgerufen und lösen Prüfabläufe aus, die alle relevanten im Prozess beteiligten Achsen und Lager der Schleifmaschine mittels Sensorik wie Schwingungsmesser, Körperschall und Kraft- und Temperaturmessung beurteilen. Hieraus lassen sich frühzeitige elektromechanische Abweichungen diagnostizieren. Wartungskosten lassen sich dadurch hinsichtlich Planung und Diagnose optimieren und potenzielle EOL Auffälligkeiten werden frühzeitig erkannt und vermieden.
Das vollintegrierte Überwachungssystem bietet bei Einbindung von Datenbanken und Cloud-Computing vernetzte Datenanalysemöglichkeit bei 100%iger Rückverfolgbarkeit und eindeutiger Zuordenbarkeit der Maschine, deren Maschinenkomponenten und individuell produzierten Werkstücke. Durch datenbasierte Verknüpfung der Erfahrung des Maschinenherstellers betreffend der Systemmechanik und des Bearbeitungsprozesses, Echtzeit-Monitoring und Datenanalyse können Wartungen mit hoher Wahrscheinlichkeit vorausgesagt werden. Auf dem webbasierten Gesamtanlagensystem werden auftretende Wartungsaufgaben farblich als Eskalationsstufen dargestellt – von Grün über Orange auf Rot. Grün beschreibt den Status „in Ordnung“, Orange meldet eine anstehende Wartung an, lässt aber zeitlich noch genügend Spielraum. Erst bei Rot wird ein Handlungsbedarf akut.
Datenaufzeichnung
Das Argus System erlaubt eine lückenlose Aufzeichnung aller am Prozess beteiligten Daten, die in einem Manufacturing Execution System (MES) zu Deutsch „Betriebsdatenerfassungssystem“, an das die Maschinen angebunden sind und wo die Daten in vollem Umfang und zeitlich unbegrenzt gespeichert werden können.
Zusammenfassung
Das Argus System zeigt, dass auch der komplexeste Schleifprozess, wie ihn das kontinuierliche Wälzschleifen von Verzahnungen darstellt, transparent und kontrollierbar gemacht werden kann. Diese Transparenz und Kontrollierbarkeit bringt nicht nur wirtschaftlichen Nutzen, sondern ermöglicht die von den Anwendern geforderte Null-Fehler-Produktion.
Quelle | Reishauer