Modellierung der Kühlwirkung beim Werkzeugschleifen - unter Berücksichtigung prozessbedingter Unsicherheiten
___Benjamin Bergmann, Klaas Maximilian Heide, Berend Denkena, Frederik Wiesener
Für die Herstellung von geometrisch bestimmten Schneidwerkzeugen, wie Schaftfräsern oder Wendelbohrern, ist das Nutenschleifen ein zentraler Bestandteil des Bearbeitungsprozesses. Ein Großteil der dabei eingebrachten mechanischen Energie wird in Wärme umgewandelt. Abhängig von den Schnittbedingungen werden dabei bis zu 95 % der Energie über das Werkstück abgeführt [1]. Die verbleibende Energie verteilt sich auf das Werkzeug, die Späne und den Kühlschmierstoff. Der Wärmestrom in das Werkstück ist besonders kritisch, da es hierdurch zu Schleifbrand und thermisch induzierten Eigenspannungen kommen kann. Dies verringert die Einsatzfähigkeit, Oberflächenqualität und Maßhaltigkeit des Werkstücks [1]. Aufgrund der Vielzahl an individuellen Korneingriffen stellt der Schleifprozess eine komplexe Eingriffssituation dar. Trotz konstanter Prozessstellgrößen sind starke Unterschiede in Prozesskräften, Kontaktzonentemperaturen und resultierenden Oberflächen zu beobachten [2]. Zurückzuführen ist dies unter anderem auf stochastische Effekte in der Schleifkontaktzone [3]. Verschleißmechanismen, wie Bindungszusetzung, Kornausbrüche und Kornabstumpfung, beeinflussen die Schleifscheibenmikrotopographie und damit den Kontakt zwischen Schleifscheibe und Werkstück erheblich [4]. Die Effektivität der Kühl- und Schmierwirkung durch den Kühlschmierstoff wird dadurch maßgeblich beeinflusst [5]. Die Einstellung von Kühlschmierstoffdüsen sowie die Wahl des passenden Schleiföls werden in der Praxis oft anhand von erfahrungsbasiertem Wissen oder zeitintensiven Einstellversuchen getroffen. Simulationen bieten hingegen eine kostengünstige Alternative, um die genannten Effekte zu prognostizieren und optimale Prozesseinstellungen zu gewährleisten. Insbesondere neuartige Herangehensweisen zur multiskaligen Prozesssimulation können bei geringer Rechenzeit das Zusammenwirken von mikroskopischen und makroskopischen Vorgängen prognostizieren [6]. Stochastische Effekte, bedingt durch einzelne Korneingriffe, werden dabei berücksichtigt, wodurch eine detaillierte Analyse des Schleifprozesses möglich ist.
Multiskalige Simulationsmethode
Das Institut für Fertigungstechnik und Werkzeugmaschinen der Leibniz Universität Hannover erforscht in Kooperation mit dem Zentrum für Industriemathematik der Universität Bremen eine multiskalige Materialabtrag-Thermofluiddynamiksimulation für das Werkzeugschleifen. Ein besonderer Aspekt ist hierbei die „unscharfe“ Betrachtung der Kühlschmierstoffverteilung und der resultierenden thermischen Werkstückbelastung in der Kontaktzone. Der Begriff „multiskalig“ bedeutet in diesem Fall, dass Vorgänge sowohl auf der Makroebene (gesamtes Werkstück und Schleifscheiben) als auch auf der Mikroebene (Teilbereich der Kontaktzone zwischen Schleifscheibe und Werkstück inkl. einzelner Schleifkörner) simuliert werden. Weiterhin findet eine Kopplung verschiedener Simulationsverfahren auf beiden Betrachtungsebenen statt. Zur Simulation des Materialabtrags kommt die recheneffiziente Materialabtragsimulation „IFW-CutS“ zum Einsatz. Zur Berechnung des Kühlschmierstoffstroms und der Temperaturausbreitung findet die FE-basierte Simulationsanwendung „FeatFlow“ Anwendung. Ziel ist es, die Vielzahl an unterschiedlichen Wechselwirkungen und deren Einfluss auf das Prozessergebnis zu erfassen, um schlussendlich Optimierungsmaßnahmen für den Schleifprozess abzuleiten.
Makrosimulation
Auf der makroskopischen Skala wird zunächst die gesamte Maschinenkinematik einschließlich der Schleifscheibe und des Werkstücks betrachtet. Die Komponenten werden auf einfache geometrische Körper zurückgeführt, um Rechenleistung sowie Rechenzeit einzusparen. Zu den Ausgangsgrößen gehören, neben der resultierenden makroskopischen Werkstückgeometrie, das Zeitspanvolumen, Gesamtspanungsquerschnitte, Kontaktflächen und lokale Eingriffsbreiten/-tiefen der Schleifscheibe (vgl. Abbildung 1 A). Da der Schleifscheibeneingriff nach Abschluss des Einfahrvorgangs über den Verlauf der Nut konstant bleibt, ist für die detaillierte Betrachtung des Prozesses auf der Mikroskala ein Teilbereich der Kontaktzone ausreichend.
Mikrosimulation
Auf der mikroskopischen Ebene wird der Prozess in Ausschnitten kornaufgelöst simuliert. Auch hier konzentriert sich die Untersuchung auf die Kontaktzone zwischen Werkstück und Schleifscheibe, jedoch mit einer deutlich höheren geometrischen Auflösung und sehr geringen Simulationszykluszeiten (vgl. Tabelle 1). Die Schleifscheibenoberfläche wird durch ein parametrisches Schleifscheibenmodell digital nachgebildet, bei dem neben der Bindungsstruktur einzelne Schleifkörner berücksichtigt werden [7] (vgl. Abbildung 1 B). Hierzu wurden Diamantkörner der Fa. L.M. Van Moppes & Sons SA (FMD-Serie) mittels Fokusvariation an einem Alicona infinite Focus G5 optisch erfasst und 3D-Modelle einzelner Körner aus den Scandaten rekonstruiert. Die stochastische Verteilung von Schleifkörnern entlang des Schleifscheibenumfangs erfolgt auf Basis der volumetrischen Zusammensetzung der Schleifscheibe. Durch die Angabe von Schleifscheibendurchmesser, -breite, Korngröße und -konzentration wird die notwendige Anzahl an Körnern berechnet. Um unterschiedliche Mikrotopographien und daraus resultierende Schärfzustände der Schleifscheibe einzustellen, wird der Abrichtprozess simuliert, indem die Schleifscheibenbindung zurückgesetzt wird. Unter der Annahme, dass aufgrund der limitierten Kornhaltekraft der Bindung bis zu 20 % des Korns aus der Bindung herausstehen kann [8], lassen sich durch die Kombination aus Bindungsrücksatz und einem einstellbaren maximalen Kornüberstand variable Schleifscheibenmikrotopographien generieren. Aufwändige Topographiescans sind hierzu nicht erforderlich. Zur Parametrierung und Validierung des entwickelten Modells wurden reale Schleifscheibenoberflächen zu unterschiedlichen Standzeiten analysiert und mit den digital erzeugten Schleifscheibenoberflächen verglichen. Weiterhin wurden resultierende Werkstückoberflächen aus Flachschleifuntersuchungen mit entsprechenden Mikrosimulationsergebnissen verglichen und anhand von Rauheitskennwerten die Prognosegüte des Schleifscheibenmodells bewertet. Abbildung 1 C, unten zeigt beispielhaft die simulierte Mikrotopographie des Werkstücks mit einer Korngröße von D54.
Durch die Mikrosimulation ist es möglich, die Eingriffsbedingungen für jedes einzelne Schleifkorn zu ermitteln. Je nach Anwendungsfall werden dabei mehr als 100.000 einzelne Körner abgebildet und Eingriffstiefen, -breiten, Einzelkornspanungsquerschnitte und Schnittvolumina berechnet (vgl. Abbildung 1 C). Durch die Anwendung eines empirischen Einzelkornkraftmodells werden Schnittkräfte und -leistungen prognostiziert (vgl. Einzelkornkraftmodellierung). Durch die Vielzahl von unterschiedlichen Körnern können stochastische Effekte, bedingt durch variierende Kornüberstände und Orientierungen, berücksichtigt werden. Auch Verschleißeffekte, wie Kornausbrüche, Abstumpfung und Bindungszusetzung sowie sprödes Materialtrennverhalten können optional in der Simulation dazugeschaltet werden. Da sich nach einer vollständigen Umdrehung der Schleifscheibe bereits alle aktiv schneidenden Körner durch die Kontaktzone bewegt haben, reichen nur wenige Umdrehungen aus, um aussagefähige Ergebnisse zu erhalten. Neben technologischen Kenngrößen, wie Eingriffstiefen und Prozesskräften, steht die resultierende Mikrotopographie des Werkstücks zur Verfügung, die in der Thermofluiddynamiksimulation zur Berechnung der Kühlschmierstoffverteilung genutzt wird. Alle Ergebnisse können schlussendlich auf die Makroskala übertragen werden, indem die makroskopischen Eingriffsbedingungen über die gesamte Kontaktzone zunächst normiert werden und anschließend für die Skalierung der Ergebnisse aus der Mikrosimulation herangezogen werden. Wie zuvor erwähnt, werden die Einzelkornkräfte und resultierenden Einzelkornschnittleistungen durch ein empirisches Kraftmodell berechnet.
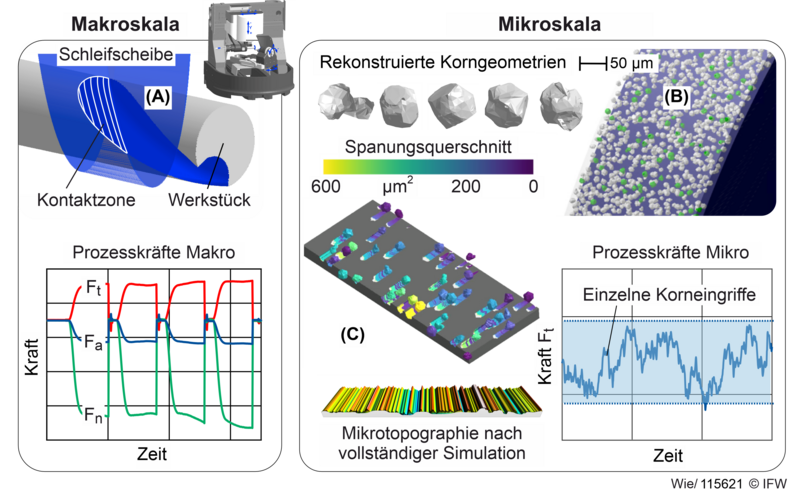
Einzelkornkraftmodellierung
Auf Basis des in der Mikrosimulation berechneten Einzelkornspanungsquerschnittes, können unter Anwendung eines empirischen Modells die Tangential- und Normalkräfte berechnet werden. Unter Berücksichtigung der Schnittgeschwindigkeit lässt sich so die resultierende Wärmeleistung am Einzelkorn berechnen. Die wirkenden Kräfte über den gesamten Schleifscheibeneingriff können in Abhängigkeit von der Zeit durch Integration über alle schneidenden Einzelkörner ermittelt werden. Zur Ermittlung notwendiger Modellkoeffizienten wurden am IFW Einzelkornritzuntersuchungen durchgeführt und die auftretenden Prozesskräfte gemessen (vgl. Abbildung 2). Zum Einsatz kommt eine Flachschleifmaschine FS 840 KT CNC der Fa. Geibel und Hotz. Eine modifizierte Schleifscheibe, bestehend aus einem Stahl-Grundkörper und einem Metallstift, trägt den Ritzdiamant, der ein einzelnes Schleifkorn der Schleifscheibe repräsentiert. Als Werkstück kommen geschliffene Hartmetall Quadratstäbe der Fa. TIGRA GmbH zum Einsatz. Die Prozesskräfte werden mit einem Kistler 9119AA2 Dynamometer erfasst. Zur Modellparametrierung werden die Schleifkräfte an der Stelle des maximalen Korneingriffs ausgewertet. Die Hartmetallprobe wird dabei leicht angestellt, sodass durch passende Kombination aus Schnitt- und Vorschubgeschwindigkeit die maximale Spanungsdicke in Vorschubrichtung variiert werden kann. Die entstandenen Ritzgeometrien wurden anschließend mittels optischer Oberflächenmessung (Nanofocus µScan) ausgewertet. Hierbei wurden die resultierenden maximalen Einzelkornspanungsquerschnitte sowie Eingriffstiefen und -breiten bestimmt werden. Durch Korrelation der Einzelkornspanungsquerschnitte mit den gemessenen Prozesskräften erfolgte die Ableitung eines empirischen Modells. Zur Modellparametrierung wurden mehr als 2.000 Ritzuntersuchungen ausgewertet. Mit einem durchschnittlichen R2 = 0,96 liefert die lineare Regression ausreichend genaue Ergebnisse zur Prognose von Tangential- und Normalkräften sowie zu der darauf aufbauenden Berechnung der Einzelkornschnittleistung [9].
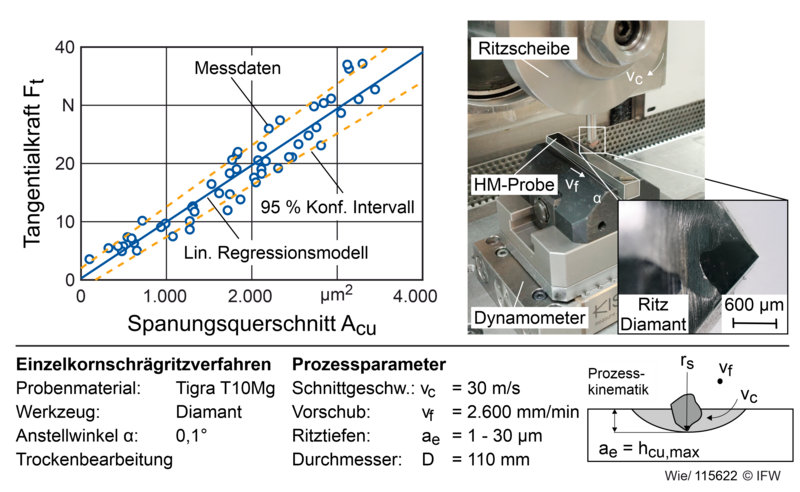
Kühlschmierstoffströmungs- und Temperaturberechnung
Zur Prognose der KSS-Wirkung und Temperaturverteilung werden die Mikrotopographien und berechneten Wärmeströme aus der Materialabtragsimulation in die Finite-Elemente-Simulation überführt. Zunächst wird auf der Mikroskala lokal der KSS-Strom im Schleifspalt simuliert. Zum Einsatz kommen dafür die Mikrotopographie der Schleifscheibe und resultierende Werkstückoberflächen. Unter Anwendung von Modellen zur Oberflächenbenetzung [10], KSS Geschwindigkeiten sowie Volumenströmen kann die Verteilung des KSS in der Kontaktzone lokal abgebildet werden. Wie zuvor werden auch diese Ergebnisse auf die Makroskala skaliert. Die rauen Oberflächen von Schleifscheibe und Werkstück werden hierzu, inklusive berechneter Benetzungseigenschaften, über mathematische Modelle beschrieben und auf die gesamte Kontaktzone erweitert [11]. Die Wirkung einzelner Körner, in Zusammenhang mit dem Schleifscheibenbindungsmaterial, kann auf diese Weise berücksichtigt werden ohne das diese geometrisch in der Makrosimulation abgebildet werden müssen. Dies reduziert die Rechenzeit signifikant. Unter Berücksichtigung der Wärmeeingangsleistung und Wärmeaufteilung auf Schleifscheibe, Werkstück, KSS und Späne können durch die Finite-Elemente-Simulationen Temperaturverteilungen für unterschiedliche Kühlbedingungen und Schleifscheibenzustände berechnet werden. Abbildung 3 zeigt den Vergleich zwischen experimentellen Untersuchungen und entsprechenden Simulationsergebnissen. Sowohl im Experiment, als auch in der Simulation wurde der Schärfzustand der Schleifscheibe durch unterschiedliche Kornüberstände charakterisiert. Abnehmende Kornüberstände führen dabei zu erhöhter Reibung und schlechterer KSS-Benetzung der Oberflächen. Es kommt zu einem signifikanten Anstieg der Temperaturen in der Kontaktzone. Dies wird nicht nur im Experiment, sondern auch in der Simulation deutlich.
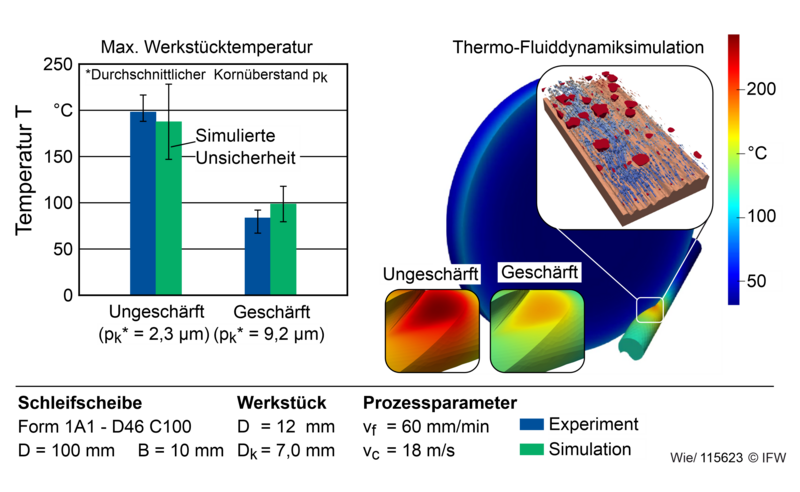
Zusammenfassung und Ausblick
Durch die zunehmende Komplexität von Werkzeuggeometrien, neuartigen Schleifscheibenbindungssystemen und Kühlschmierstoffzusammensetzungen steigt der Bedarf an Simulationslösungen zur Auslegung und Planung von Werkzeugschleifprozessen. Dabei stellt die Optimierung von Kühlschmierstrategien, insbesondere in Hinblick auf Nachhaltigkeit und Energieeffizienz, einen großen Hebel zur Steigerung der Wirtschaftlichkeit dar. Im Rahmen des DFG-Schwerpunktprogramms 2231 wurden die hier vorgestellten Methoden und Modelle zur multiskaligen Prozesssimulation erarbeitet und werden in den kommenden zwei Jahren finalisiert. In der dritten und letzten Förderphase des Projekts liegt der Fokus auf der Anwendung des Systems zur multiskaligen Prozessanalyse und -optimierung. Geplant sind beispielsweise weiterführende experimentelle Studien zum KSS-Strömungsverhalten und thermomechanischer Belastung der Kontaktzone. Auch das vorgestellte Schleifscheibenmodell wird fortlaufend erweitert, um zukünftig den Zustand der Mikrotopographien dynamisch, in Abhängigkeit von der Standzeit, zu prognostizieren. Auf diese Weise sollen Abrichtzyklen geplant werden und eine optimale Schleifwerkzeugauswahl, je nach Anwendungsfall, erfolgen.
Quelle | IFW Hannover